Starting an Air Compressor: A Step-by-Step Guide
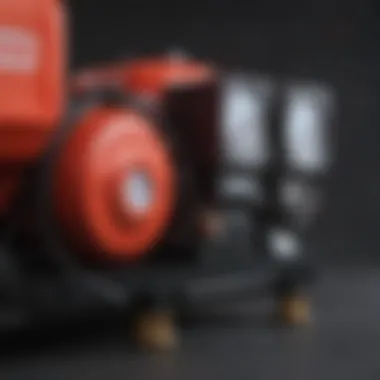
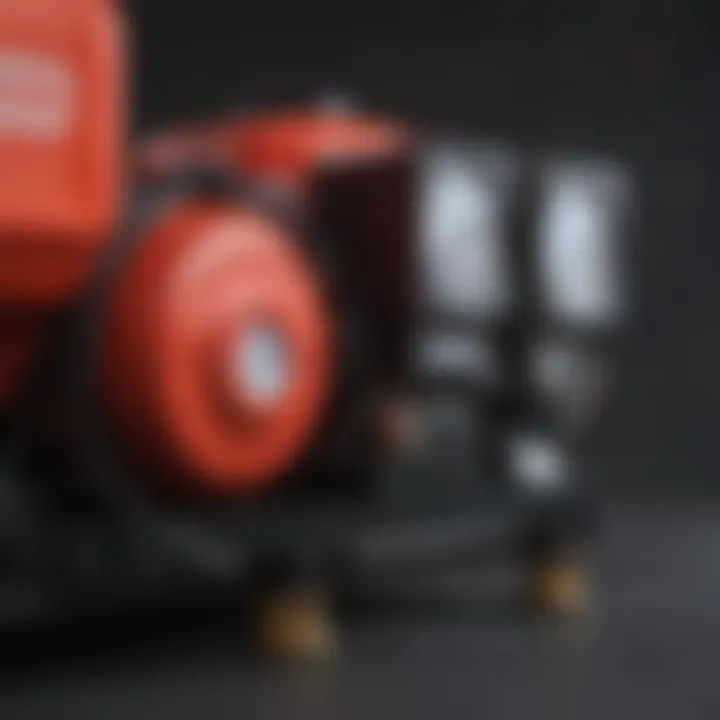
Intro
Air compressors are vital tools, particularly in agriculture, where they assist with various tasks such as powering tools, inflating tires, and even spraying pesticides. Understanding how to start an air compressor efficiently is crucial for optimal performance and safety. This guide will delve into the essential steps and best practices for launching an air compressor, allowing users to maximize its potential in their daily operations.
Overview of the Topic
Definition and Importance
An air compressor is a device that converts power into potential energy stored in pressurized air. This pressurized air can then be used to operate pneumatic tools, paint sprayers, and more. The significance of air compressors lies in their ability to provide a reliable source of power across various applications. For farmers and agricultural workers, air compressors are indispensable for boosting productivity.
Current Trends
In recent years, there has been a marked shift towards more energy-efficient and portable air compressor models. Electric air compressors are gaining popularity, as they reduce operational costs and are eco-friendly. Additionally, advancements in technology have led to quieter models, which is a significant benefit for farmers operating near livestock or residential areas.
Key Techniques and Practices
Step-by-Step Guide
Starting an air compressor involves several methodical steps to ensure safe and effective operation:
- Check the Oil Level: Ensure that the oil level is adequate as low oil can damage the compressor.
- Inspect the Air Filter: A clean air filter promotes efficiency. If dirty, it should be cleaned or replaced.
- Connect to Power Source: Ensure the compressor is connected to the appropriate power source, whether it be an electrical outlet or a generator.
- Set the Pressure Regulator: Adjust the pressure regulator to the required PSI depending on the tool being operated.
- Start the Compressor: Turn on the power switch and monitor the pressure gauge as the compressor builds pressure.
- Check for Leaks: Once it reaches the desired pressure, inspect for any air leaks around the hose or connections.
Tools and Equipment Needed
To operate an air compressor safely and effectively, ensure you have the following tools and equipment:
- Pressure gauge
- Wrenches for adjusting connections
- Air hoses compatible with the compressor
- Safety goggles and gloves to protect against pressure hazards
Challenges and Solutions
Common Obstacles
While starting an air compressor may seem straightforward, there are common obstacles that users encounter:
- Insufficient Air Pressure: This can occur due to leaks or incorrect settings.
- Electrical Issues: Problems may arise with power supply or connections interrupting functioning.
- Overheating: Continuous operation without breaks can cause overheating and trigger safety shutdowns.
Innovative Solutions
Addressing these issues requires specific strategies:
- Regular maintenance checks can prevent many issues related to air pressure.
- Ensuring that electrical connections are secure and compatible can mitigate electrical failures.
- Allowing the compressor periodic breaks can prevent overheating, thus extending its life.
"Proper usage and maintenance can significantly improve the lifespan and efficiency of air compressors."
By following these guidelines, users can enhance their expertise in handling air compressors, ensuring safe operation and prolonging the equipment's longevity. A thorough understanding of air compressors not only improves safety but also optimizes performance in agricultural endeavors.
Intro to Air Compressors
Air compressors play a crucial role in numerous industries, including construction, manufacturing, and agriculture. Understanding their functioning and applications can significantly enhance efficiency and productivity. This section delves into the core definition and functionality of air compressors, as well as their significance in agriculture and horticulture.
Definition and Functionality
An air compressor is a device that converts power into potential energy stored in pressurized air. It utilizes a motor to drive a piston or a similar mechanism, compressing the air into a storage tank. Once compressed, the air can be released on demand to perform various tasks. The process of compression not only increases pressure but also decreases the volume of the air. This flexibility makes air compressors indispensable tools in settings that require pneumatic power.
Typically, air compressors fall into two categories: positive displacement and dynamic compressors. Positive displacement compressors work by trapping a specific amount of air and then reducing its volume, while dynamic compressors rely on high-speed rotation to draw in and compress air. Common applications include powering pneumatic tools, inflating tires, and spraying paint. Understanding these basic functions is essential for users who wish to start and operate air compressors safely.
Importance in Agriculture and Horticulture
The agricultural sector benefits substantially from air compressor systems. They are commonly used for tools such as pneumatic drills, irrigation systems, and agricultural machinery. The efficiency provided by compressed air enables farmers to operate tools with precision, improving productivity. Moreover, the ability to spray fertilizers and pesticides using air compressors promotes more even application, which can lead to healthier crops and higher yields.
In horticulture, air compressors facilitate various tasks including soil aeration and watering. Compressed air systems can help manage irrigation effectively, ensuring water reaches where it is most needed without waste. Moreover, the capability to power tools for pruning and harvesting enhances the speed and efficiency of these labor-intensive tasks.
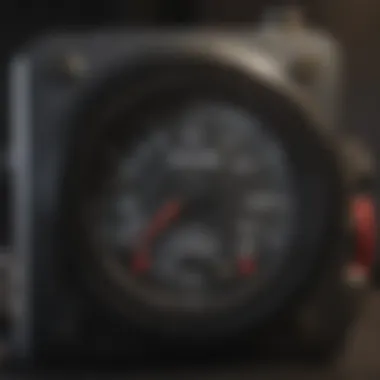
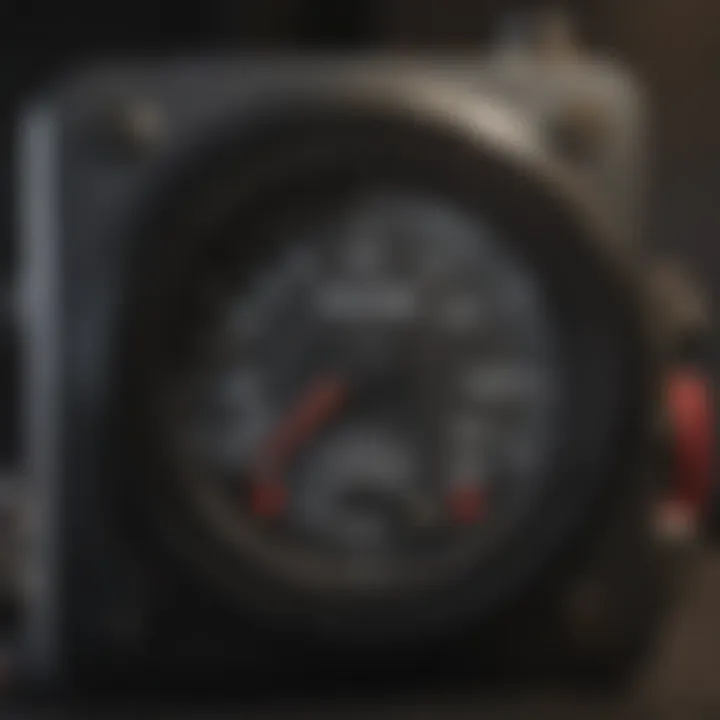
Air compressors are not just mechanical devices; they are integral to advancing modern agricultural practices.
Types of Air Compressors
Understanding the different types of air compressors is crucial for users, especially in agriculture. Each type serves specific needs and offers distinct advantages based on various operational requirements. Choosing the right type can enhance efficiency and productivity, making it a vital topic in this guide.
Reciprocating Air Compressors
Reciprocating air compressors are widely used due to their effectiveness in generating high pressure. These compressors use a piston driven by a crankshaft to compress air, making them highly efficient for tasks that require consistent pressure. They are often found in small workshops and agricultural settings, providing a reliable source of compressed air for various tools and equipment.
One of the key benefits of reciprocating compressors is their versatility. They can operate in both single-stage and two-stage configurations, depending on the required pressure levels. In agriculture, they are commonly used for powering pneumatic tools, inflating tires, and spraying pesticides. However, maintenance is essential as these compressors can be louder and may require regular oil changes to maintain performance.
Rotary Screw Compressors
Rotary screw compressors operate using a pair of rotors to compress air, offering a continuous flow of air. These are ideal for applications that require a steady output, such as in large farming operations or construction sites. Their design allows for efficient airflow and can handle larger volumes of air compared to reciprocating types.
An advantage of rotary screw compressors is their lower maintenance needs. They have fewer moving parts and often come equipped with features like automatic shut-off systems, enhancing safety. However, they may come with a higher initial cost, which can be a consideration for smaller farms or businesses.
Centrifugal Compressors
Centrifugal compressors are typically used in large industrial applications but can be beneficial in specific agricultural contexts. They utilize a rotating disk to generate high-speed airflow, converting kinetic energy into pressure. These compressors are ideal for high-flow applications.
The primary benefit of centrifugal compressors is their ability to handle large volumes of air, making them perfect for extensive farming operations or facilities that demand a significant air supply. Maintenance is essential, but they tend to operate quietly. Still, due to their complexity, they are best suited for larger-scale operations where performance needs justify the investment.
Choosing the right type of air compressor can significantly affect operational efficiency and cost-effectiveness in agricultural applications.
Preparation Steps Before Starting
Preparing to start an air compressor is crucial for safety and efficiency. Proper preparation can prevent accidents and ensure optimal performance during operation. By examining various elements such as safety protocols and equipment checks, users can gain more confidence and knowledge in operating their air compressor effectively. Below are key steps that should never be overlooked.
Understanding Safety Protocols
Safety should always be the first consideration when operating an air compressor. Familiarizing oneself with safety protocols can significantly reduce the risk of accidents. This includes wearing appropriate personal protective equipment like safety goggles and gloves.
Before starting, one must ensure that the surrounding area is free from any obstructions or flammable materials. Additionally, consulting the user manual specific to your air compressor model will provide tailored safety information, which varies among different brands and types.
Following safety guidelines not only protects the operator but also prolongs the machine’s lifespan by preventing damage caused by misuse.
Checking the Oil Levels
Oil level is integral to the performance and longevity of your air compressor. Insufficient oil can lead to increased friction, causing overheating and permanent damage to internal components. Checking the oil level should be part of your routine maintenance.
To check the oil:
- Locate the oil dipstick on your compressor.
- Remove it and clean it with a cloth.
- Reinsert it and remove again to check the oil level against the markings.
If you find the oil is below the recommended level, make sure to refill it with the correct type of oil, as specified in your compressor’s manual.
Inspecting Air Hoses and Connections
Hoses and connections are critical components of an air compressor system. Damaged or worn hoses can cause air leakage, which reduces efficiency and can lead to higher operating costs. It's important to carry out a visual inspection of all hoses and connections before turning on the compressor.
During the inspection:
- Look for signs of wear, such as cracks or cuts.
- Ensure that all connections are tight and free from obstructions.
Repair or replace any damaged hoses immediately to prevent operational failures during use.
Verifying the Power Supply
Finally, it is vital to ensure that the power supply is adequate and operational before starting the compressor. Confirm that the electrical outlet can support the power requirements of your air compressor model. An inadequately powered compressor can lead to erratic performance or even electrical failure.
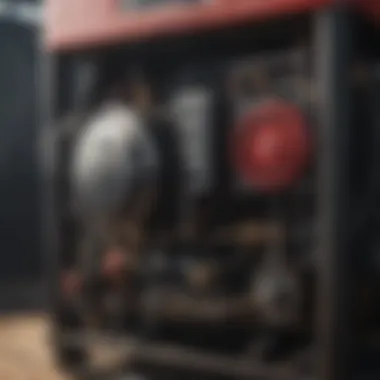
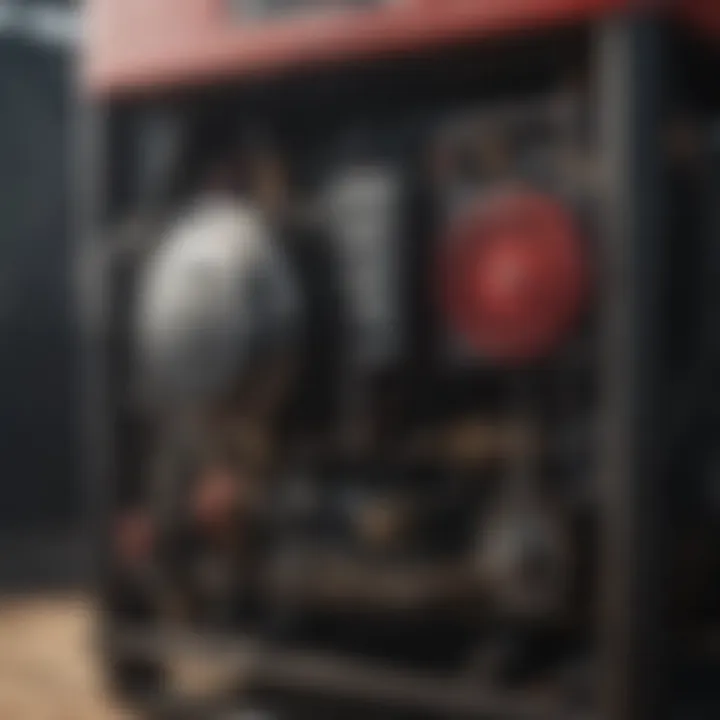
Check the following:
- Ensure that the power cord is intact and in good condition.
- Confirm that the circuit breaker is functioning properly and can handle the necessary load.
By methodically performing these checks, one can ensure the air compressor starts smoothly and runs efficiently, thus enhancing productivity.
Starting the Air Compressor
Starting the air compressor is a pivotal step in effectively utilizing this essential equipment. This process not only determines the operational efficiency but also ensures an optimal safety standards during use. When set up correctly, starting the air compressor becomes a straightforward task that enables users to harness compressed air for various applications, particularly in agriculture and horticulture.
When beginning the ignition process, it is important to follow specific steps. Neglecting any of these protocols can lead to issues, including machinery damage or even personal injury. Therefore, understanding the elements associated with turning on the air compressor involves careful attention to operation manuals and the manufacturer’s guidelines. This section will unpack the necessary steps to consider when starting the machine, ensuring both safety and performance.
Turning on the Power Switch
The first action in starting an air compressor is engaging the power switch. This hardware component controls the flow of electricity to the compressor motor. Before doing this, users should ensure that the machine is properly connected to the power supply. Confirming the connection eliminates the risk of power failure when attempting to start the compressor.
Once you identify the power switch, it is straightforward to turn it on. However, be mindful to only use the switch designated for this purpose. In several models, the switch may be located near the control panel, designed for easy access. Turn it to the "on" position; you should see indicators or lights that denote the machine is receiving power.
Important: Always verify that you are wearing appropriate personal protective equipment before handling electrical components.
Setting the Pressure Regulator
Following the activation of the power switch, the next critical task is to set the pressure regulator. This component plays a significant role in controlling the output pressure of the air compressor. Setting it correctly is crucial, as output pressure influences efficiency and safety during operation.
To set the pressure properly, consult the manufacturer’s specifications regarding the optimal pressure levels for specific tasks. Adjust the pressure regulator dial or lever based on this information. Typically, users can increase or decrease the pressure with simple adjustments. Moreover, watch for the pressure gauge, which displays the current output pressure. Setting it too high can lead to equipment damage, while too low may not meet operational needs.
Checking for Unusual Noises
After ensuring that the power is on and the pressure has been set, users must listen for any unusual noises from the compressor. Normal functioning should include the sound of the motor and airflow without abnormal vibrations or knocking sounds. Listening to the compressor can indicate underlying issues that may need addressing before further operation can occur.
If there are unusual noises, it may stem from several sources: misaligned components, lack of lubrication, or internal wear and tear. In this case, stop the compressor and reassess the equipment. It is advisable to consult the troubleshooting guide in the user manual, as it typically provides solutions tailored to specific models. Addressing these concerns promptly is essential to avoid potential breakdowns or safety risks.
Common Issues When Starting
Starting an air compressor can be a straightforward task when the proper steps are followed. However, it is essential to recognize potential obstacles that may arise during the process. Understanding these common issues is crucial for ensuring safety, optimizing performance, and achieving efficient operation.
Awareness of common issues allows users to troubleshoot effectively. This knowledge not only saves time but also prevents further damage to the compressor. Let's delve into some of the most frequent problems users may encounter when attempting to start their air compressor.
Power Failure
Power failure is perhaps the most critical issue when starting an air compressor. If the compressor does not power on, the problem could lie with the power source. First, check the outlet where the compressor is plugged in. Ensure that the outlet is functional by testing it with another device. If the compressor still does not start, inspect the power cord for visible signs of wear or damage. It may also be necessary to check the compressor's internal fuse or circuit breaker.
Often, power failures stem from a lack of proper connections or a blown fuse. Ensuring that all electrical connections are secure is fundamental. Additionally, using a surge protector can prevent power fluctuations that might damage the compressor's electrical components.
Pressure Problems
Pressure issues can manifest in various forms, affecting the overall functionality of the air compressor. If the compressor starts but does not build pressure, it may indicate a problem with the pressure switch or regulator. Ensure that the pressure settings are correctly configured, adjusting them if necessary to meet specific operational needs.
Low pressure can lead to insufficient power for tools and other equipment reliant on compressed air. Monitoring the compressor's pressure gauge regularly helps identify problems before they escalate.
In some situations, excessive pressure may build up, leading to safety risks. It is vital to understand the compressor's specifications and operating limits to avoid such scenarios. Regular stewardship of the compressor ensures safe and efficient use.
Leakage Issues
Leakage can significantly reduce the efficiency of an air compressor. Air leaks can occur in various components, including hoses, fittings, and couplers. Identifying the source of a leak is vital for maintaining performance. When starting an air compressor, listen for hissing sounds or feel for air escaping around hoses and connections.
It may help to apply a soap solution to suspected areas to reveal leaks, as bubbles will form where air escapes. Once identified, replace or repair any faulty parts to restore the compressor’s efficiency. Regular maintenance, including inspection of all connections and seals, plays a vital role in preventing leaks.
The efficiency of an air compressor is only as good as its ability to maintain pressure and functional connections.
Addressing these common issues when starting an air compressor is essential in achieving optimal results. By knowing how to troubleshoot power failures, pressure problems, and leakage issues, users can ensure their compressors operate effectively. This not only saves time but also enhances the longevity of the equipment, making it a vital aspect of air compressor operation.
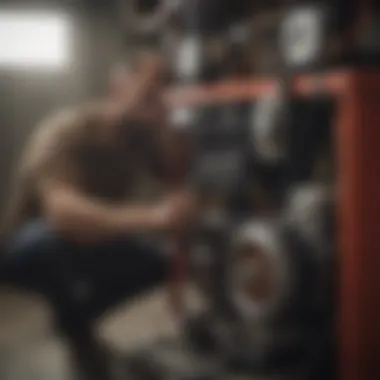
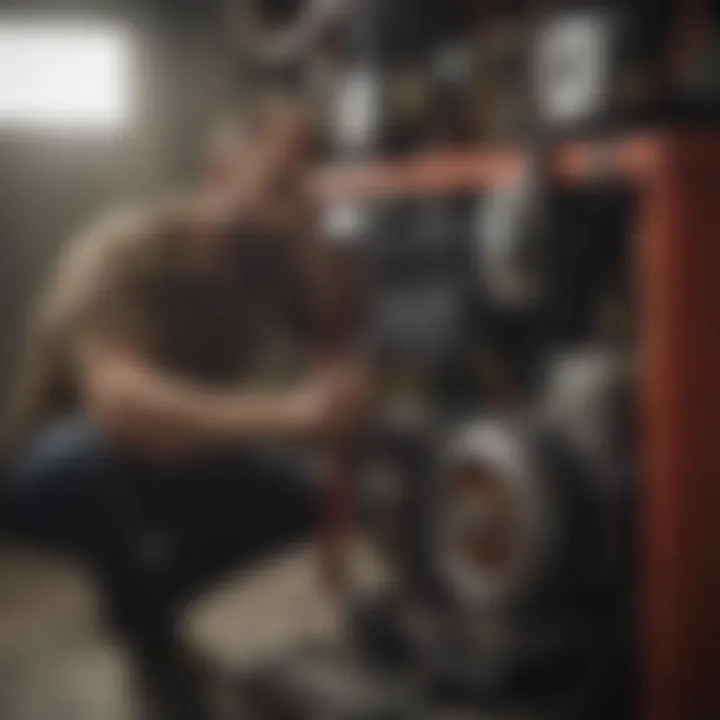
Troubleshooting Guide
In any operational machinery, understanding how to troubleshoot issues is crucial for maintaining performance and preventing downtime. This section focuses on the troubleshooting guide specific to air compressors. The significance of this guide cannot be overstated—it empowers users to identify problems swiftly, implement solutions effectively, and ensure continued functionality of their equipment. Familiarizing oneself with common difficulties faced can lead to enhanced efficiency and increased safety for both the operator and the machine itself.
Identifying the Problem
The first step in troubleshooting an air compressor is accurately identifying the problem. Several symptoms may signal an issue, including:
- Inconsistent pressure output: Fluctuations in pressure can degrade performance.
- Unusual noises: Sounds that differ from the normal operation may indicate mechanical issues.
- Frequent tripping of circuit breakers: This can signify electrical faults or overloads.
Careful observation is essential. Operators should remain attentive to their equipment's behavior during and after use. Ignoring subtle signs can lead to more significant problems down the line. The objective is to gather as much information as possible to assist in diagnosing the issue, whether it be through visual inspection or performance data.
Step-by-Step Troubleshooting
Once the problem is identified, a methodical approach to troubleshooting can help in diagnosing and resolving the issue.
- Power Off the Compressor: Ensure that the machine is turned off and disconnected from power to avoid accidents before starting any troubleshooting steps.
- Check the Manual: Refer to the manufacturer's manual for specific guidance concerning the symptoms observed. Manuals often include troubleshooting sections tailored to the specific model.
- Examine Key Components:
- Test Electrical Connections: Ensure that all electrical connections are secure. Loose wires can cause intermittent faults, often leading to bigger issues.
- Run a Diagnostic: If equipped, some compressors have built-in diagnostic modes. Utilizing these can provide valuable information about internal errors or faults.
- Repair or Replace: Depending on the issue's nature, repairs may involve tightening hoses, replacing faulty components, or even seeking professional assistance for complex issues.
- Pressure Switch: Inspect for any signs of malfunction which can affect the pressure settings.
- Hoses: Look for cracks or wear that could lead to leaks. A damaged hose can severely affect compressor operation.
- Oil Levels: Verify that oil levels are adequate. Low oil can lead to increased wear and tear.
Following these steps not only helps in resolving current issues but can also provide insight into maintenance practices to prevent future occurrences. For further related discussions, consider exploring topics on related forums or websites such as reddit.com or the manufacturer's Facebook page.
Maintenance for Longevity
Proper maintenance of an air compressor is vital for ensuring its longevity and optimal performance. Air compressors are often employed in agriculture and other demanding environments, requiring them to operate efficiently. Regular maintenance minimizes the risk of unexpected failures that can disrupt operations. Furthermore, it can enhance energy efficiency and reduce overall operating costs. The following aspects of maintenance are key: oil changes, air filter cleaning, and inspecting belts and hoses.
Regular Oil Changes
Oil changes are essential for the health of an air compressor. The oil lubricates the internal components, reducing friction and wear. Over time, the oil can become contaminated with dirt, debris, and moisture, which diminishes its effectiveness. For maximum performance, it is recommended:
- Check the oil level before each use.
- Change the oil according to the manufacturer's guideline, typically every 50 to 100 hours of operation or as indicated by the oil condition.
- Use the right type of oil specified in the user manual.
Regular oil changes not only enhance performance but also prevent costly repairs, making it a critical practice in air compressor maintenance.
Cleaning the Air Filter
The air filter plays a crucial role in protecting the engine and components of the air compressor from dust and debris. A clean air filter helps maintain efficient airflow, contributes to optimal performance, and reduces strain on the motor. Therefore, it is important to:
- Inspect the air filter before operation and clean it if necessary.
- Replace it when it shows signs of wear or clogging, usually every few months or as needed.
A clean air filter can boost productivity and extend the life of your compressor, ensuring it operates at peak efficiency.
Inspecting Belts and Hoses
Belts and hoses are integral to the operation of an air compressor. Timing belts ensure the proper functioning of compressors, while hoses deliver compressed air to tools and machinery. Regular inspection can prevent unexpected breakdowns. It is advisable to:
- Check belts for signs of wear, such as cracks or fraying. Replace them if needed.
- Inspect hoses for leaks, abrasions, or signs of wear. Replace any damaged sections immediately.
Regular checks on belts and hoses contribute to sustained performance, ensuring that the compressor operates without unnecessary interruptions.
Overall, regular maintenance is not just a practice; it is a necessity. Well-maintained air compressors lead to better performance and longer service life.
Finale
In this article, the conclusion serves as a crucial summary of the overall guidance on starting an air compressor effectively. The importance of this topic cannot be overstated, particularly in the context of optimizing operational efficiency in agriculture. An air compressor is an invaluable tool in various agricultural practices, from powering pneumatic tools to operating irrigation systems. Understanding how to start and maintain such a device fosters not only safety but also extends its operational lifespan, making it more cost-effective in the long run.
Summary of Key Points
- Understanding Types of Compressors: Familiarity with different air compressor types, such as reciprocating, rotary screw, and centrifugal, is essential. Each type has its advantages and suitables applications.
- Preparation Steps: Adhering to safety protocols, checking oil levels, inspecting air hoses, and verifying power supply are critical before ignition. These steps prevent potential hazards.
- Starting Procedures: Properly turning on the power switch, setting the pressure regulator, and listening for unusual noises ensure successful startup.
- Troubleshooting Common Issues: Recognizing power failures, pressure problems, and leakage can prevent operational interruptions.
- Maintenance Practices: Regular oil changes, cleaning air filters, and inspecting belts contribute to the longevity of the air compressor.
Future Considerations
As technology advances, the efficiency and functionality of air compressors will continually improve. Future users should stay informed about innovative compressor models and upgrades. For farmers, integrating more energy-efficient equipment can enhance operational sustainability. Additionally, understanding evolving safety standards will help ensure compliance and reduce risks.
Engaging in community forums or groups on platforms like Reddit and Facebook can provide invaluable insights into user experiences and tips, further enhancing one's expertise in air compressor management.
Staying ahead in compressor technology and maintenance will result in better investment returns and improved productivity in agricultural practices.