Effective Methods for Loosening Rusted Bolts Safely
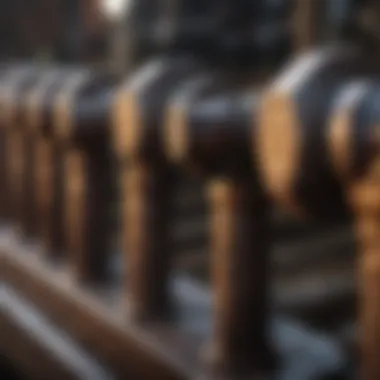
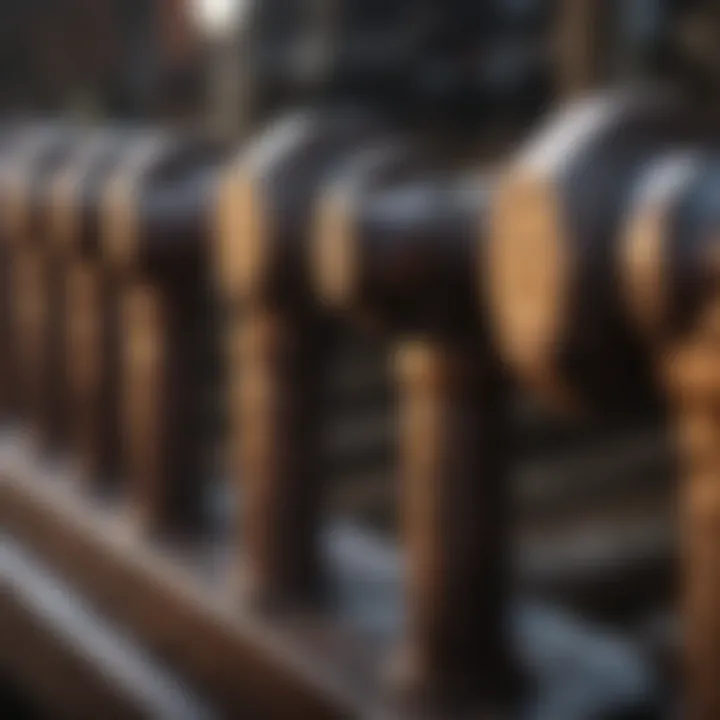
Overview of the Topic
Definition and Importance
Loosening rusted bolts is a common challenge faced by professionals and enthusiasts in agriculture, mechanical work, or DIY projects. When equipment or machinery sits idle for extended periods, moisture and rust can set in, leading to bolts becoming stuck. This can hinder repair and maintenance, ultimately affecting efficiency. Understanding the methods and techniques to loosen these bolts is vital for preventing potential equipment failure or damage. A systematic approach can save time and avoid unnecessary frustration.
Current Trends
There is a growing awareness of both mechanical and chemical methods to address rusted bolts. Modern innovations, such as specialized penetrating oils and advanced tools, have emerged in the market. Farmers and agricultural workers increasingly seek solutions that are not only effective but also safe and environmentally friendly. This reflects a broader trend toward sustainability in farming practices, ensuring that maintenance tasks are carried out without harm to the environment.
Key Techniques and Practices
Step-by-Step Guide
When addressing rusted bolts, a strategic step-by-step process is essential:
- Assess the Situation: Determine the extent of rust and the type of bolt. Consider the equipment's material and any surrounding components that may be affected.
- Clean the Area: Remove any dirt, debris, or grease around the bolt. A clean working environment aids in better observation and application of techniques.
- Apply Penetrating Oil: Use a penetrating oil like PB Blaster or WD-40. Apply generously and allow it to sit for an adequate time, typically 15-30 minutes or longer if heavily rusted.
- Use Mechanical Force: Attempt to turn the bolt with a wrench. If the bolt does not move, avoid excessive force that could break it. Instead, try tapping the bolt gently with a hammer or using a breaker bar.
- Heat Application: As a last resort, an application of heat with a heat gun or torch can expand the metal, allowing for easier loosening.
Tools and Equipment Needed
The toolbox for loosening rusted bolts should contain several key items:
- Penetrating Oil: Essential for breaking down rust.
- Wrenches or Socket Sets: Various sizes are necessary for different bolt types.
- Breaker Bar: To provide additional leverage.
- Heat Source: A heat gun or torch for advanced cases.
- Hammer: For gently tapping and applying force.
- Wire Brush: For cleaning rust from surfaces.
Challenges and Solutions
Common Obstacles
Rusted bolts may resist removal due to several factors:
- Severity of Rust: Thick layers of rust create a bond that requires more effort to overcome.
- Access Issues: Some bolts may be located in hard-to-reach places, complicating the process.
- Breaking or Stripping Bolts: Excess force can lead to stripped threads or broken bolts, causing further repair challenges.
Innovative Solutions
To mitigate these challenges, enthusiasts can explore innovative solutions:
- Ultrasonic Cleaners: These devices can help in loosening bolts without direct mechanical force.
- Chemical Rust Removers: Products that chemically dissolve rust can be effective when combined with mechanical methods.
- Professional Help: Sometimes, the most effective solution is to consult a professional, especially for high-value equipment where damage risk is significant.
"Prevention is often more efficient than repairing damage. Regular maintenance can prevent rust from setting into bolts."
By understanding these methods and challenges, both agricultural professionals and enthusiasts alike can effectively confront the issue of rusted bolts. Ensuring that proper techniques and tools are used is critical not only for the success of maintenance tasks but also for the longevity of equipment.
Understanding Rusted Bolts
Rusted bolts are a significant concern in agriculture and maintenance. Understanding why bolts rust develops a foundation for addressing the issue effectively. Rust can cause various operational challenges. These challenges can hinder equipment performance and result in safety risks. Knowing the factors contributing to rust formation and the implications helps in the prevention and resolution of these problems.
Causes of Rust Formation
Rust formation occurs due to a combination of various elements. These include environmental factors, material composition, and mechanical stress. Each aspect plays a vital role in how and when rust develops on bolts.
Environmental Factors
Environmental factors substantially influence rust formation. High humidity, exposure to water, and temperature fluctuations encourage oxidation. When moisture interacts with iron, rust develops when oxygen bonds are broken. This aspect is crucial to understanding rust because it highlights how conditions contribute to the problem.
- Key characteristic: Moisture is the primary catalyst for rust.
- Contribution: Areas with high humidity levels often encounter more rust issues due to inadequate protection against moisture. An awareness of these factors aids in selecting appropriate storage and usage methods to minimize rusting.
- Advantages: By monitoring and controlling environmental conditions, one can reduce the risk of rust formation.
Material Composition
The material composition of bolts also impacts rust susceptibility. Different alloys and surfaces have varying levels of resistance to corrosion. Steel bolts, for example, are more prone to rust than stainless steel or galvanized bolts. Understanding this aspect allows for better material selection based on the working environment.
- Key characteristic: Different materials respond differently to rusting.
- Contribution: Using materials that resist rust can extend the lifespan of tools and machinery. This choice is important for maintaining functional equipment and reducing replacement costs.
- Advantages: Investing in higher-quality materials can prevent frequent rust-related issues, allowing for smoother operations.
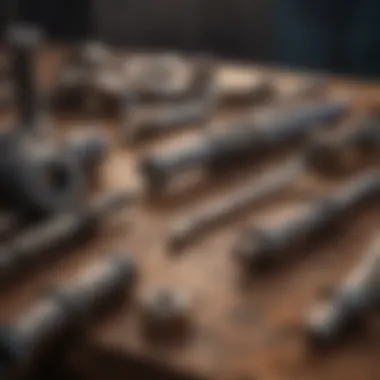
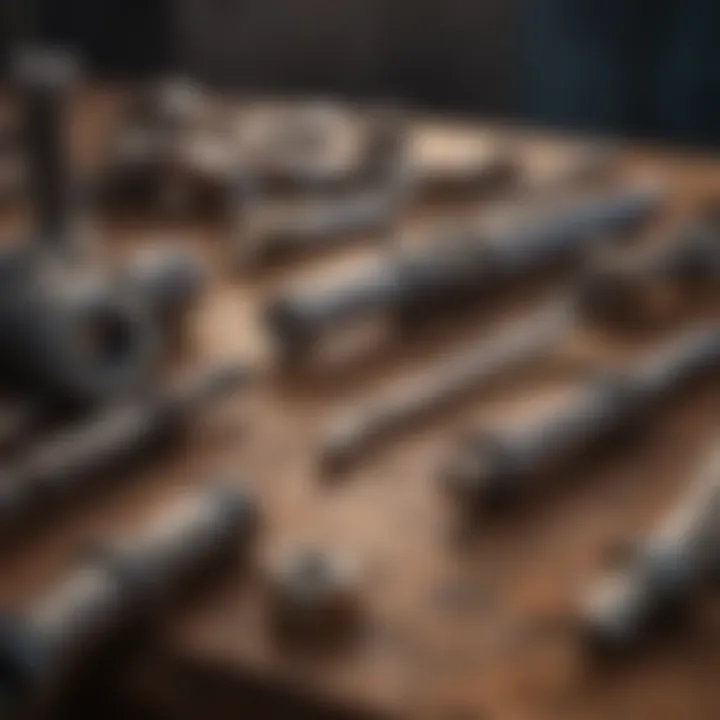
Mechanical Stress
Mechanical stress is another crucial factor in rust formation. When bolts undergo stress from forces such as tension or compression, it can lead to surface damage that predisposes them to rust. Damaged surfaces are more likely to allow moisture infiltration, accelerating corroding processes.
- Key characteristic: Failure points in bolts often arise from wear and mechanical strain.
- Contribution: Understanding how stress affects materials can inform maintenance protocols, ensuring that bolts remain robust under load.
- Advantages: Proper assessments and routine checks can identify stressed bolts before they rust, preventing complete failure.
Implications of Rusted Bolts
Rusted bolts present various implications in agricultural settings. These implications highlight the need for prompt assessment and corrective actions to maintain safety and functionality.
Impact on Equipment Functionality
Rust can severely impact the functionality of equipment. When bolts corrode, they become weaker and less reliable. A rusted bolt can fail under stress, leading to potential equipment breakdown. This can result in costly downtimes.
- Key characteristic: Not all rusted bolts lead to immediate failure, but they reduce overall reliability.
- Contribution: With affected functionality, operations may be interrupted, causing delays in tasks that depend on that equipment. Understanding this allows operators to prioritize inspections.
- Advantages: Regular maintenance checks can help identify rust problems early and prevent equipment failure.
Potential Safety Hazards
Beyond functionality, rusted bolts pose serious safety hazards. The failure of a corroded bolt can lead to accidents, endangering both operators and nearby persons. The risk of equipment, such as tractors and machinery, malfunctioning is crucial.
- Key characteristic: The sudden failure of critical components can lead to uncontrolled situations.
- Contribution: Recognizing the risks associated with rust can make professionals more vigilant. This awareness can inform training practices in handling tools and equipment.
- Advantages: Taking preventive measures reduces potential safety issues, thereby protecting individual workers and larger communities.
In summary, understanding rusted bolts is essential for agricultural professionals. Knowledge about the causes and implications can lead to effective decision-making in maintenance and operations, ultimately enabling smoother processes in the field.
Initial Assessment Before Attempting to Loosen a Bolt
Assessing the condition of a rusted bolt before any physical attempt to loosen it is critical. This stage serves as the foundation for applying appropriate techniques and tools effectively, minimizing the risk of equipment damage and enhancing safety. By focusing on both visual indicators and the specifics of the bolt's specifications, one can identify the best approach for successful removal.
Importance of initial assessment lies in recognizing potential challenges and tailoring methods accordingly. It can help to avoid common pitfalls that lead to ineffective results or further complications, such as snapping a bolt or damaging surrounding components.
Visual Inspection
Identifying Signs of Corrosion
Identifying signs of corrosion is essential in evaluating the state of a rusted bolt. Corrosion can significantly weaken the bolt, making it both difficult to remove and potentially dangerous. Key characteristics of corrosion often include a reddish or brownish film, flaking or pitting on the surface, and a rough texture.
Recognizing these signs informs the user of the right method for extraction. The benefit of assessing corrosion levels is that it provides insight into the extent of damage, which may require more aggressive techniques or solutions. Ignoring these symptoms can lead to further issues during the loosening process.
Evaluating Bolt Integrity
Evaluating bolt integrity goes hand-in-hand with corrosion assessment. This involves checking for any visible damage such as bending, cracking, or significant wear. Understanding the integrity of a bolt can guide the operator in choosing the right tools and methods to apply.
A well-integrated evaluation can prevent unnecessary force application, which may lead to breakage. This careful assessment is advantageous in ensuring that safe methods are prioritized, minimizing risks to both the operator and equipment during removal.
Determining Bolt Type and Size
Metric vs. Imperial Bolts
Determining whether a bolt is metric or imperial is crucial for selecting the correct tools and avoidance of stripping threads. Metric bolts are measured in millimeters, while imperial bolts use inches. The differences in sizing can significantly affect grip and leverage when attempting to loosen a bolt.
This knowledge helps avoid using incorrect tools that could slip and cause damage. Each type has its unique specifications, making it necessary to identify the correct system used. Failure to do so can lead to complications in the removal process, underscoring the importance of precise identification.
Understanding Thread Patterns
Understanding thread patterns of bolts is vital for those planning to loosen them. Thread patterns influence how tools engage with the bolt. Knowing whether the thread is coarse or fine aids users in choosing the appropriate socket or wrench for the job.
This aspect is significant because it can affect both fit and torque application. Effectively identifying thread patterns allows for a more secure grip, decreasing the chances of damaging the bolt further. A correct understanding of this technical detail can streamline the working process, making it easier and safer to remove a rusted bolt.
Mechanical Methods to Loosen Rusted Bolts
Mechanical methods to loosen rusted bolts are critical in situations where chemical solutions do not provide the needed leverage or may take too long to work. These techniques employ physical force and tools to address the stubbornness of rusted bolts effectively. They are essential for mechanics, DIY enthusiasts, and agricultural professionals who face such challenges in their day-to-day tasks. Proper mechanical methods can greatly reduce the time and effort necessary for removal, preventing damage to equipment and promoting safety.
Using Leverage
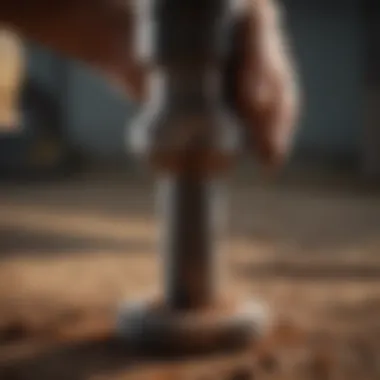
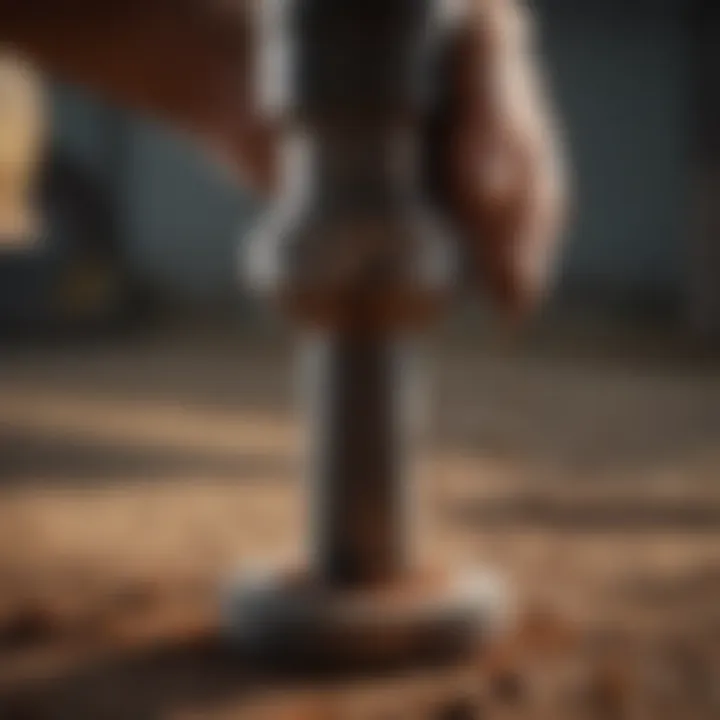
Using leverage is a foundational mechanical technique for loosening rusted bolts. Leverage multiplies the force applied, enabling the user to break free a bolt that has become stuck due to rust. This method is often preferred for its simplicity and effectiveness.
Adjustable Wrenches
Adjustable wrenches are versatile tools that can grip various sizes of nuts and bolts. Their key characteristic is the ability to adapt to different sizes, making them suitable for various tasks. When loosening a rusted bolt, they allow for precise fit without the need to have multiple wrenches on hand. This adaptability is a strong advantage, especially in environments like farms or workshops where tool variety may be limited. However, one must be cautious about slippage. Improper adjustment can lead to ineffective grip and could cause damage to the bolt or nut.
Breaker Bars
Breaker bars are designed specifically for applying maximum torque to loosen bolts. The unique feature of a breaker bar is its length, which provides additional leverage compared to regular ratchets. This tool excels at freeing stubborn bolts, making it a popular choice amongst professionals. Its length allows for greater force application, reducing strain on the user's hands and wrists. The disadvantage might include the requirement of enough space to maneuver, which can be a limitation in tight spots.
Impact Tools
Impact tools are powerful mechanical devices that provide quick bursts of high torque to loosen bolts. They are particularly effective where rust has created a strong bond between the bolt and the surrounding material.
Socket Impact Wrenches
Socket impact wrenches are high-torque electric or pneumatic tools designed to quickly remove rusted bolts. Their key characteristic lies in their ability to deliver rapid and intense force that loosens bolts efficiently. They are indispensable for tasks requiring speed and substantial torque, making them a beneficial choice in many mechanical settings. A notable advantage of using socket impact wrenches is their ease of use, but they can be more expensive than manual tools, which may deter some users.
Impacts vs. Ratchets
The debate between impacts and ratchets largely hinges on the type of task being performed. Impacts provide powerful, sudden bursts of energy, ideal for rusted bolts that resist traditional turning methods. In contrast, ratchets offer a smooth, consistent turning motion that can be effective for less resistant hardware. The real advantage of impacts for this article is their ability to combine power and speed, while ratchets shine in situations demanding finesse or in confined spaces. Knowing when to use each tool can dramatically impact the success of the task at hand.
Tap and Hammer Technique
The tap and hammer technique leverages focused impacts to disrupt the rust bond. It is a hands-on method that emphasizes precision and control in applying force.
Using a Hammer
Using a hammer adds impact force to the removal process. This method involves tapping the bolt to break the rust seal gently. The key characteristic of this technique is the low risk of damaging surrounding materials, which makes it suitable for delicate machinery. It provides a beneficial option in situations where other methods may not be advisable. However, significant caution is required; too much force can still lead to damage. Overall, it is effective for rust that has not progressed too far.
Application Technique
The application technique refers to how one should implement the tap and hammer method effectively. A focused approach, with the hammer striking directly at the center of the bolt head, is crucial. This key characteristic allows for optimal energy transfer, making looseness more achievable. The use of an appropriate size hammer is also important; too light may not perform effectively, while too heavy might cause damage. This technique shows great advantage in environments where mechanical methods are less feasible.
Heat Application
Heat application is a powerful technique to loosen rusted bolts, relying on thermal expansion to break the bond formed by rust.
Propane Torches
Propane torches are widely used for applying heat to stubborn bolts. The key characteristic of propane torches is their ability to produce high temperatures quickly. By heating the bolt, the metal expands, often breaking the rust's grip. This method is especially useful in tight spots, where leverage cannot be effectively applied. However, they require caution; high heat can damage threads or the surrounding material if not handled wisely.
Cautions with Heat
Using heat requires careful consideration. The key characteristic of these cautions includes awareness of flammable materials nearby and potential for thermal damage. Always ensure the area is safe and free from hazards before applying heat. While this method can be highly effective, it carries risks, so having a clear plan and understanding the specifics of the hardware involved is crucial. Properly applied, heat can turn the tide on even the most stubborn rusted bolts.
Chemical Methods for Loosening Rusted Bolts
Chemical methods for loosening rusted bolts play a crucial role in addressing rust-related issues effectively. Unlike mechanical methods, which rely on physical tools and techniques, chemical applications focus on breaking down rust and grime to facilitate easier bolt removal.
Utilizing chemicals can save time and reduce the physical effort required, especially in challenging situations where mechanical methods may prove to be ineffective. However, this strategy requires careful consideration and a proper understanding of the products and techniques involved.
Penetrating Oils
Popular Products
Penetrating oils are at the forefront of chemical methods for loosening rusted bolts. These products are designed to seep into rust and corrosion, breaking the bond that holds the bolt in place. Some well-known penetrating oils include WD-40, PB Blaster, and Liquid Wrench.
The key characteristic of these popular products is their ability to penetrate tight clearances that typical lubricants cannot reach. This makes them a beneficial choice for loosening rusted bolts, especially in environments where corrosion is persistent. The unique feature of penetrating oils is their formulation, which utilizes lighter viscosity oils that can flow into rusted joints. The advantage of this method is significant; penetrating oils can often provide results without excessive force or destructive actions on the surrounding material.
Application Techniques
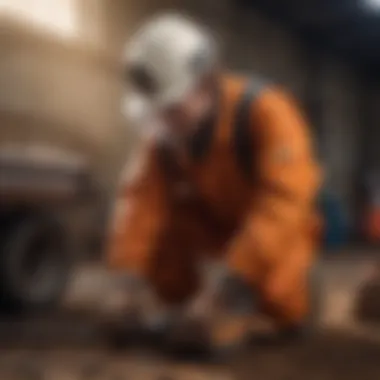
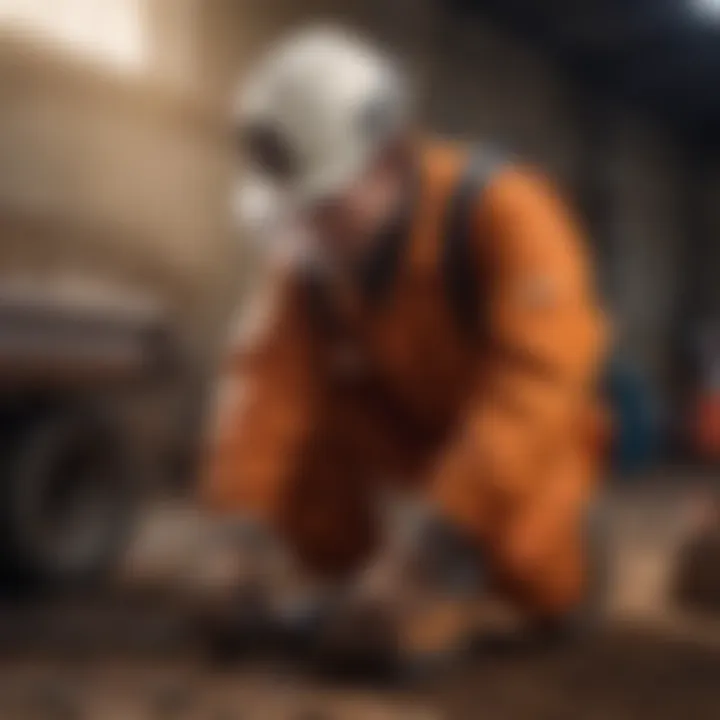
Application techniques for penetrating oils are integral to their effectiveness. The common approach involves spraying the oil directly onto the rusted bolt and allowing it to sit for a period of time—typically 10 to 30 minutes—so it has enough time to work into the corrosion.
A critical factor for successful application is ensuring the area is as clean as possible before applying the oil. A clean surface allows the oil to penetrate better. Additionally, it is important to apply enough product to saturate the rusted area fully.
The advantage of this technique is that it requires minimal equipment, usually just the can of penetrating oil and sometimes a cloth to remove excess oil. However, the disadvantage may include varying effectiveness based on the severity of rust and sometimes longer wait times than expected.
Homemade Solutions
Acetic Acid Mixtures
Acetic acid mixtures, commonly found in vinegar, present a natural solution for loosening rusted bolts. The acidic environment created by acetic acid works to break down rust over time, making it easier to remove bolts.
A key aspect of using acetic acid mixtures is their accessibility. Most households have vinegar on hand, making it a popular choice for many users. Acetic acid is beneficial as it is non-toxic and relatively safe compared to harsher chemical options. The unique feature of this solution is its ability to lift away corrosion without damaging the underlying metals. However, the disadvantage is that it may require prolonged soaking to achieve significant results.
Vegetable Oil Blends
Vegetable oil blends represent another homemade option for loosening rusted bolts. Mixing vegetable oil with other agents such as baking soda can enhance its lubricating properties and create a protective barrier against further rust.
The primary appeal of vegetable oil blends lies in their non-toxicity and environmental friendliness. They are easy to prepare and utilize with readily available kitchen ingredients. The advantage of this method is low cost and minimal harm to the environment or metal surfaces. However, one should note that vegetable oil might not penetrate as deeply as commercial penetrating oils, requiring repeated applications to achieve desired success.
In summary, chemical methods for loosening rusted bolts, whether through commercial penetrating oils or homemade solutions, provide effective alternatives to mechanical methods. Trial and error with these methods may lead to finding the best solution for each unique situation.
Preventive Measures and Maintenance
Preventive measures and maintenance play a crucial role in ensuring the longevity and functionality of bolts, especially in agricultural settings where rust may cause significant delays and safety hazards. Understanding these measures is essential for professionals and enthusiasts alike, as they not only aid in avoiding challenges associated with rusted bolts but also contribute to the efficient operation of machinery and tools. Proper preventive actions can save time and resources by minimizing the likelihood of rust formation, thus ensuring that bolts remain in optimal condition for extended periods.
Regular Inspections
Schedule Maintenance Checks
Scheduling regular maintenance checks is vital for early identification of rust issues. This proactive measure enables individuals to detect corrosion before it escalates into more severe problems. The key characteristic of these checks is that they establish a routine, reducing the chances of overlooked issues. Regular inspections help track the condition of bolts and associated machinery, making it a popular choice among agricultural professionals. A unique feature of scheduled maintenance checks is the ability to develop a consistent inspection routine, which ensures that all components are scrutinized systematically. One advantage of this practice lies in its preventive capacity, as it can significantly reduce unplanned equipment failures. However, if not conducted diligently, there is a risk of missing critical indicators of rust.
Documentation Practices
Documenting inspection results is another essential aspect. This practice contributes to a clearer understanding of the condition and history of each bolt and equipment. The key characteristic is the creation of a reliable record that can be referred to during future assessments. Documentation is a beneficial choice because it creates a detailed account of previous rust issues, repairs, and preventive measures undertaken. A unique element of this practice is the ability to analyze recurring patterns in equipment degradation, fostering better-focused maintenance strategies. While keeping records enhances accountability and responsiveness, it can also require time and diligence to maintain.
Proper Lubrication
Best Practices for Lubrication
Employing best lubrication practices is equally important in preventing rust. Proper lubrication reduces friction, limits moisture ingress, and creates a protective barrier against corrosive elements. The key characteristic of best practices is their strategic application, ensuring that every bolt receives adequate protection. This practice is beneficial as it significantly extends the lifespan of bolts and associated machinery. A unique feature is that implementing best practices can also improve equipment performance, allowing for smoother operation. One downside is that improper application can lead to buildup, which may attract dirt and debris if not managed correctly.
Choosing the Right Lubricant
Selecting an appropriate lubricant is a critical decision. The right lubricant contributes directly to maintaining a protective film on bolts. The defining characteristic is the compatibility with the materials used in the bolts and surrounding components. Making informed choices about lubricants is beneficial because each type offers distinct properties suited for various environmental conditions. For example, some lubricants excel in high-temperature settings while others are ideal for damp conditions. A unique aspect is the shift to biodegradable or environmentally friendly options, which many farmers prefer nowadays. However, the ongoing availability and effectiveness of certain specialized lubricants may pose challenges.
Conclusion: Implementing preventive measures, documenting inspections, and maintaining proper lubrication are essential strategies to combat rusted bolts. These practices create a foundation for effective maintenance and reliable operations. By adopting a detailed approach, agricultural professionals can significantly improve the reliability and safety of their equipment.
Epilogue
Understanding how to effectively loosen rusted bolts is a critical aspect of maintenance and repair, particularly within agricultural settings. The techniques discussed throughout this article provide a diverse toolkit for encountering these stubborn fasteners. It is important to consider the combination of mechanical and chemical methods, as they can each serve a unique purpose depending on the severity of rust and the tools available.
Recap of Techniques
To summarize, the methods for loosening rusted bolts are multifaceted:
- Mechanical Methods: Leveraging tools such as adjustable wrenches and impact wrenches demonstrate how applying physical force can break the rust bond effectively. The tap and hammer technique also adds value by loosening debris and corrosion build-up. Heat application introduces expansion that can help free bolts that are set in harsh conditions.
- Chemical Methods: Products like penetrating oils can dissolve rust effectively. Homemade solutions using items like acetic acid mixtures also serve as viable options for those who prefer not to use store-bought chemicals.
- Preventive Measures: Regular inspections and proper lubrication can prevent the reoccurrence of rusted bolts. By implementing proper stored practices and maintenance checks, the likelihood of facing rust issues can be significantly reduced.
This recap underscores the necessity of employing these techniques and being ready to adapt them according to the specific situation involving rusted bolts.
Encouragement for Practical Application
The most significant takeaway from this article is the encouragement to apply these techniques in real-life situations. While the methods sound straightforward in theory, practical experience can greatly enhance your confidence and effectiveness when dealing with rusted bolts.
Start with simple rusted components in your equipment; this will allow you to understand how much force or chemical application is needed. As you gain experience, challenge yourself with more difficult scenarios. Your familiarity with each method will improve over time, leading to better outcomes and less frustration.
Remember to always prioritize safety; using proper tools and protective gear is essential to avoid injuries when handling rusted bolts or using potentially dangerous chemicals. The knowledge gained here is not only beneficial for your equipment but can also save you time and effort in the long run.
"Regular application of these techniques can protect your equipment and enhance its lifespan. Implementation is the key to efficient maintenance."