In-depth Guide to Quicke Loader Joystick Parts
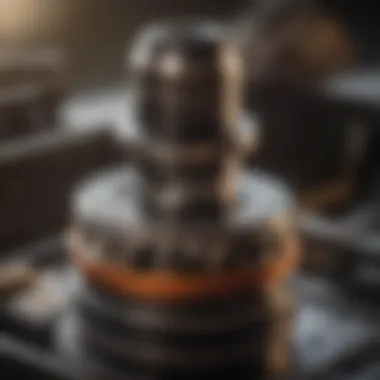
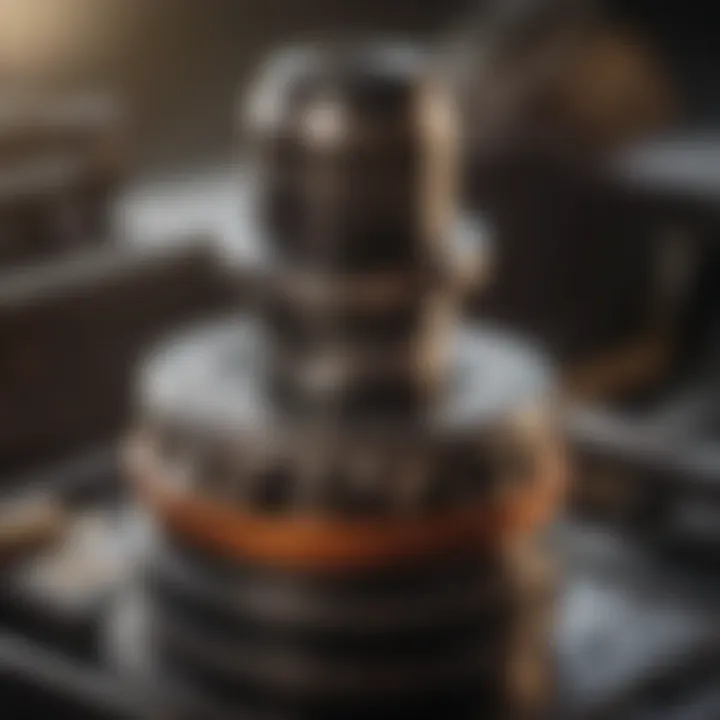
Intro
Understanding the intricate components of Quicke loader joystick systems is essential for anyone engaged in agriculture. These joysticks serve a vital role in operating loaders, enhancing efficiency and user experience. As the agricultural industry evolves, so does the technology behind these joystick systems, making it crucial to analyze their parts and functionalities in detail.
Overview of the Topic
Definition and Importance
A loader joystick is a control device that allows operators to manage various functions of the loader effectively. It enables precise movements and adjustments, which are essential for tasks like lifting, tilting, and dumping materials. The significance of a well-functioning joystick cannot be overstated. It directly impacts the overall performance of the loader and, by extension, the productivity of farming activities.
Current Trends
Recent advancements in technology have led to innovations in joystick design. Wireless technologies and ergonomic shapes are gaining popularity. Users are looking for joysticks that not only enhance control but also reduce fatigue during prolonged use.
Key Techniques and Practices
Step-by-Step Guide
- Identify the components: Familiarize yourself with the major parts of the joystick, such as the handle, base, and electronic connections.
- Assess functionality: Understand how each part contributes to the overall operation. For instance, the movement of the handle translates to specific loader actions.
- Regular maintenance: Implement a routine maintenance schedule to ensure all parts are in good working condition. This may include checking the wiring, lubricating moving parts, and testing the responsiveness of the joystick.
Tools and Equipment Needed
- Screwdriver set
- Lubricating oil
- Multimeter for electrical testing
- Cleaning cloths
These tools are crucial for routine maintenance and troubleshooting any issues that arise.
Challenges and Solutions
Common Obstacles
Users often face various challenges, including sticky controls, unresponsive movements, and wear and tear on components. These issues can severely disrupt operations and lead to decreased productivity.
Innovative Solutions
- Regular inspections: Routine checks can catch problems early.
- Upgrading parts: Replacing worn components before they fail can prevent larger issues.
- Training and education: Educating users on proper joystick handling can enhance longevity.
"Investing time in understanding and maintaining joystick systems will pay dividends in productivity and safety."
Prelude to Quicke Loaders
Quicke loaders have carved out a crucial niche in modern agriculture, serving as indispensable tools for efficiency and productivity on farms. This section explores the importance of Quicke loaders and their impact on agricultural practices. Knowledge of these loaders is fundamental for anyone involved in farming, as they directly improve the handling of materials and contribute to overall operational effectiveness.
History and Evolution
The development of Quicke loaders dates back several decades. Originally designed to aid in manual labor, these machines have evolved significantly. The first models focused primarily on basic lifting functions. Over time, as technology advanced, Quicke began incorporating more sophisticated features. This evolution mirrors the growth of the agricultural sector itself, which required better solutions for increasing productivity.
These loaders have transitioned from mechanical designs to sophisticated hydraulic systems. This shift allows for enhanced precision and capability, essential in today's demanding agricultural landscape. Additionally, Quicke loaders today often integrate advanced electronics and sensor technologies, further expanding their utility.
Importance in Modern Agriculture
In contemporary agriculture, Quicke loaders represent more than just tools; they embody the principles of efficiency and effectiveness. Farmers often face diverse tasks that require quick and accurate handling of heavy materials. This is where Quicke loaders excel.
The benefits of using Quicke loaders include:
- Versatility: They can be used in various applications, such as loading feed, moving soil, and managing supplies.
- Time-Saving: With quicker material handling, farmers can allocate time to other essential operations.
- Increased Safety: Modern loaders often have features that minimize the risk of accidents during operation.
"Using Quicke loaders has transformed the way we work on the farm. The efficiency they provide allows us to focus on growth and sustainability."
Moreover, as farming aims for sustainability, Quicke loaders support this goal by enhancing operational efficiency and diminishing physical strain on workers. Thus, they play a vital role in ensuring that modern agriculture meets the challenges of production and sustainability.
Understanding these loaders, therefore, sets a strong foundation for discussions about joystick functionality and parts, as effective handling begins with high-quality equipment.
Understanding Joystick Functionality
Understanding joystick functionality is essential for grasping how Quicke loaders operate efficiently. The joystick acts as the primary interface between the operator and the machinery, translating user input into precise actions. It directly influences operational effectiveness and user comfort. Learning about joystick functionality helps in maximizing productivity and minimizing the likelihood of operational errors.
Basic Principles of Operation
The basic principles of operation of a joystick revolve around its design and control mechanisms. At its core, a joystick operates on the principle of translating directional movements into electrical signals. This communication is vital as it enables the loader to respond accurately to the operator’s commands.
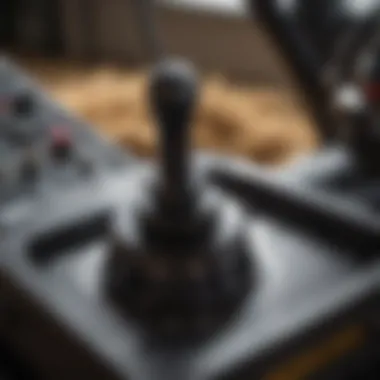
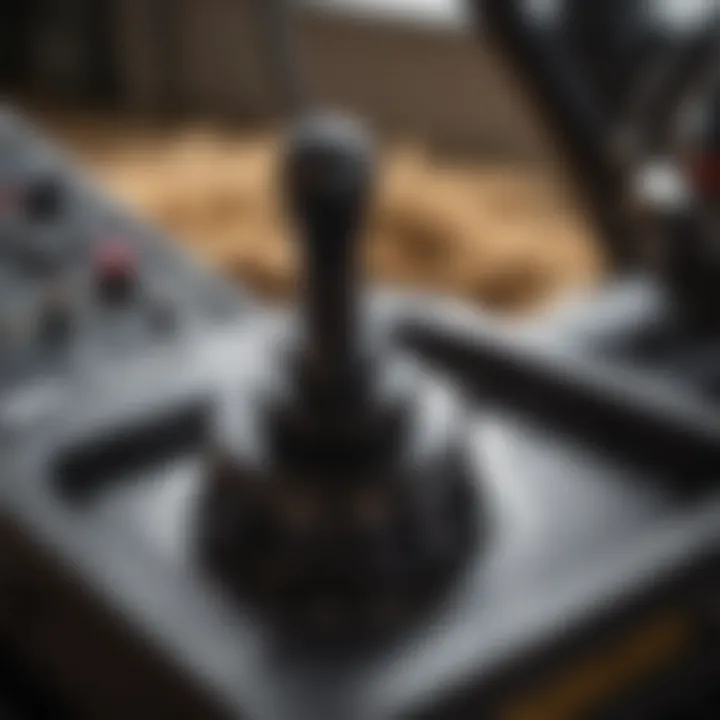
Typically, two-dimensional movement is covered, with the joystick providing control over the loader's functions such as lifting, tilting, and extending. Sensors within the joystick detect the position and movements, converting them into electrical signals that engage specific hydraulic functions. One major advantage of this type of system is its intuitiveness, allowing users to control complex tasks with minimal effort.
Types of Joystick Control Systems
There are several types of joystick control systems that one might encounter in Quicke loaders, each with its own features and benefits. Understanding these systems can help operators choose the right one for their specific needs.
- Analog Joystick Systems
These systems use variable resistors that change resistance with joystick movement. This system is straightforward but requires more maintenance due to mechanical wear and tear. - Digital Joystick Systems
Utilizing electronic circuits, digital joysticks provide more precision in signal control. They typically require less maintenance since they do not rely on moving parts. - Proportional Control Joysticks
Proportional joysticks adjust the hydraulic or electrical output based on how far the joystick is moved. This system is excellent for tasks that need precise control, making it favorable in intricate agricultural operations. - Multi-Axis Control Systems
These systems allow the control of multiple loader functions simultaneously. They are ideal for complex tasks and provide flexibility in operations, enhancing overall performance.
Choosing the appropriate joystick control system can significantly affect the user experience. Factors include the complexity of tasks, operator training level, and applications within agricultural practices. By understanding the strengths of different systems, operators can enhance their operational efficiency.
Key Components of Quicke Loader Joystick
In any joystick system, the individual components play a crucial role in determining functionality and performance. For the Quicke loader joystick, understanding these components is essential not just for users but also for those involved in the design and maintenance of agricultural equipment. By dissecting each part, we can better appreciate how they work together to facilitate smooth and efficient operation.
Control Lever
The control lever is the heart of the joystick system. It serves as the primary interface for operators, allowing them to manipulate loader actions with precision. The design of the control lever must be ergonomic, ensuring comfort during prolonged use. Materials used for the lever also affect durability; commonly, high-strength plastics or metals are employed to withstand the rigors of agricultural environments.
An effective control lever should provide a responsive feel. This helps the operator maintain total control over lifting, tilting, and other functions. Misalignment or damage to the control lever can lead to unresponsive actions or excessive strain on the user’s hands.
Electronic Circuitry
The electronic circuitry integrated into Quicke load joysticks is vital for converting mechanical movements into electronic signals. This circuitry operates the hydraulic system of the loader and affects how smoothly it responds to user inputs. It typically includes microcontrollers and various components that process input signals.
Modern developments have introduced advanced features, including programmable settings for different functions. This allows for greater customization to meet specific operating needs. However, these benefits also necessitate a higher level of maintenance and understanding of the system's intricacies. A fault in the electronic circuitry can compromise performance, making it essential for operators and technicians to be familiar with basic electrical principles.
Sensors and Feedback Mechanisms
In contemporary designs, sensors play a pivotal role in providing operators with real-time feedback on the loader's status. These sensors can detect the position and speed of the control lever, ensuring that the associated mechanical actions correspond accurately with user inputs. Advanced systems might incorporate load sensors, providing critical data that helps optimize lifting capacity and stability.
Feedback mechanisms, such as vibration or audio signals, can enhance user awareness regarding the performance of the loader. They inform operators when specific thresholds are reached, preventing potential overloading or damaging conditions. Understanding these components is key for agricultural professionals focused on maximizing productivity while ensuring the longevity of their machines.
Mounting Brackets and Accessories
Mounting brackets are not just supporting structures; they enable proper installation and alignment of joystick assemblies with other components. The choice of materials and design of these brackets can greatly impact the stability and comfort of use. Accessories, such as protective covers, can also enhance durability by shielding these components from adverse weather or debris common in agricultural settings.
Adding accessories such as grips can also impact ergonomics, making the joystick easier and more comfortable to operate. Technicians should consider both the mountings and accessories in maintenance routines to ensure the joystick functions optimally.
The effectiveness of the joystick heavily depends on how well its components synergize to create a seamless user experience.
Understanding the key components in detail allows users to make informed decisions regarding their maintenance, upgrades, and troubleshooting techniques. This level of comprehension can lead to improved operational efficiencies, ultimately benefiting productivity on the field.
Maintenance of Joystick Parts
Maintenance is critical for assuring the efficiency and lifespan of Quicke loader joystick systems. Neglecting regular upkeep can lead to improper function, reduced responsiveness, and even costly repairs. Thus, understanding how to properly maintain joystick parts is essential for optimal performance in agricultural settings.
Routine Inspections
Conducting routine inspections is the first step in maintaining joystick parts. These inspections should focus on various components, such as the control lever and electronic circuitry. Farmers should look for any signs of wear or damage, which can appear as frayed wiring or loose connections. Checking the sensors and feedback mechanisms is equally important. Any irregular behavior should be noted, as it may indicate a need for further investigation.
Secure handling during inspections can prevent additional damage. Always ensure that the equipment is powered down before examining the joystick. A well-documented inspection schedule can help keep track of potential issues before they escalate. For example:
- Regularly check wiring connections. Confirm they are not loose or damaged.
- Inspect for physical wear. Look at the joystick and its components for signs of fatigue.
- Test functions intermittently. Ensure responsiveness aligns with expected performance.
Cleaning and Care Procedures
Cleaning is a straightforward yet vital component of joystick maintenance. Dirt, dust, and debris can affect the performance of joystick parts. An effective cleaning routine involves more than basic wiping; it requires thorough attention to detail. Start by disconnecting power to the joystick. Use a soft cloth dampened with a mild cleaner to gently wipe surfaces. Avoid solvents that may corrode plastics.
Using compressed air can help remove debris from tight spaces around buttons or the control lever. Additionally, pay close attention to the electronic circuitry and connectors. They can gather dust over time, which may hinder functionality. Doing this regularly can significantly enhance the joystick's responsiveness and lifecycle.
Troubleshooting Common Issues
Troubleshooting is an important skill for Quicke loader users. Common issues arise, such as unresponsive controls, erratic movements, or sensor malfunctions. Identifying these issues quickly can save time and resources.
Some key steps include:
- Check power supply. Ensure that the joystick is receiving adequate power and that connections are secure.
- Inspect for software updates. Sometimes, the issue may lie in outdated firmware controlling the joystick.
- Run diagnostic tests. Many modern systems feature built-in tests that can help identify faults.
When addressing common complaints, focus on understanding how joystick parts work together. Oftentimes, the issue may not be isolated to a single component but rather a combination of factors affecting overall operation.
Regular maintenance can prevent minor issues from becoming significant problems and ensures that the joystick operates at peak performance.
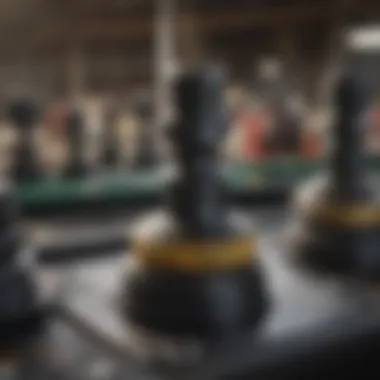
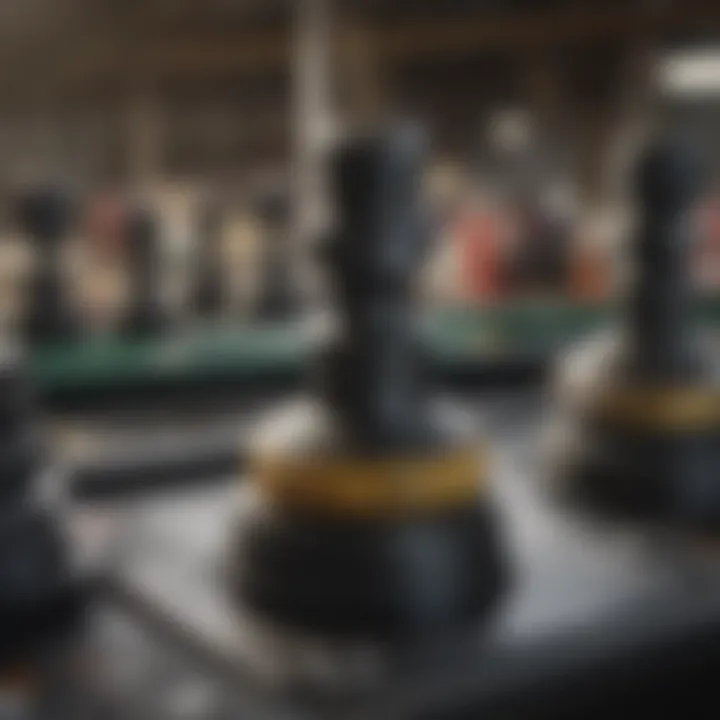
Ultimately, maintaining joystick parts requires a proactive approach. Regular inspections, diligent cleaning, and effective troubleshooting enhance system reliability. This attentiveness not only improves performance but also extends the longevity of the Quicke loader joystick system.
Selecting the Right Joystick Parts
Selecting the correct joystick parts for Quicke loaders is a critical topic. The right components can significantly affect performance and user experience. Understanding how to choose the right parts is essential for achieving optimal operation of the loader. This section delves into three main considerations: compatibility, quality versus cost, and supplier reliability.
Compatibility Considerations
When it comes to selecting joystick parts, compatibility is the first factor to examine. Each joystick is designed to work with specific models and configurations of Quicke loaders. Certain features may not align with others if the parts do not match correctly. This misalignment can lead to failures in operation and functionality.
Key points to keep in mind include:
- Model Specifications: Ensure the parts are designed for the specific loader model.
- Connector Types: Different joystick systems may use various connections. Verify that the connectors are compatible.
- Electrical Specifications: The electrical requirements should match. This can include amperage and voltage ratings for electronic components.
Failing to consider compatibility can result in wasted time and resources. It can also cause safety risks if components do not operate correctly.
Emerging Technologies in Joystick Design
The evolution of joystick systems in Quicke loaders is not just about usability. Emerging technologies play a critical role in enhancing the performance and efficiency of these systems. They represent a convergence of innovation that addresses the challenges faced by farmers and operators while improving their overall work experience. These advancements aim to integrate better functionality, increased precision, and expanded capabilities into joystick designs, which is essential for meeting modern agricultural demands.
Advancements in Sensor Technology
Modern joystick systems utilize advanced sensors to improve feedback and control accuracy. These sensors translate the user's inputs into precise commands for the loader. Several types of sensor technologies are now commonplace, including capacitive and resistive sensors, which detect the slightest movements of the joystick lever. This can result in smoother and more responsive operation.
Moreover, improved sensor technology can minimize the likelihood of mechanical failure. For instance, non-contact sensors reduce wear and tear, enhancing longevity and reliability. Furthermore, integrating sensor data with digital processing can enable real-time analysis of the joystick's performance. This leads to tailored adjustments based on specific task requirements. Farmers benefit from this as it can significantly increase efficiency while reducing operational errors.
Integration with Smart Farming Solutions
The linkage of joystick systems to smart farming solutions represents a vital shift in agricultural technology. Quicke loader joysticks now have the capability to connect with GPS systems, telematics, and specialized agricultural software. This integration allows for a more data-driven approach in field operations, promoting precise execution of tasks like material handling, spreading, and lifting.
For example, using joystick input in conjunction with GPS data enables automated controls for precise positioning and movement. This helps in maximizing productivity while minimizing resource waste. Additionally, operators can use data analytics to monitor the effectiveness of their joystick controls.
Here are some key benefits of this integration:
- Enhanced precision and speed of operations.
- Better data collection for performance assessment.
- Improved decision-making through real-time data.
- Increased safety as automated systems can reduce the risk of human error.
"The consistency offered by smart farming solutions can transform traditional farming practices, leading to a sustainable future."
In summary, emerging technologies in joystick design are more than just enhancements. They represent a fundamental shift toward smarter, safer, and more efficient agricultural practices. As farmers embrace these innovations, they facilitate not only improved labor but also a significant step towards sustainable farming.
Case Studies of Quicke Loader Use
The exploration of case studies in the context of Quicke Loader use is essential to reinforce understanding of the joystick's real-world applications. These studies provide concrete examples that illustrate the functionality, benefits, and performance of Quicke loaders equipped with joystick systems. By analyzing actual scenarios, readers can gain valuable insights into the practical operation of these loaders across various agricultural settings.
Field Performance Analysis
Field performance analysis focuses on how Quicke loaders and their joystick systems perform under different operational conditions. This assessment helps to understand how joystick design influences effectiveness during various tasks, such as lifting, moving, and manipulating materials.
Data collected from various field tests often reveal the responsiveness and precision of joystick controls. For example, farmers using Quicke loaders for heavy-duty tasks report a noticeable efficiency in maneuverability, especially in tight spaces. Feedback from users indicates that the joystick aids in maintaining control over the loader's actions, which is especially important when handling delicate tasks like placing bales without damaging crops.
"The Quicke loader's joystick allows me to navigate my fields with accuracy. I can move quickly and confidently, knowing I won't damage my plants." - A farmer's testimonial.
Furthermore, these studies often compare various loading tasks, assessing both speed and user-friendliness. The joystick's ergonomic design enhances operator comfort during extended periods of use, contributing to overall productivity levels.
Comparative Study with Other Brands
A comparative study provides a perspective on how Quicke loaders stack up against competitors. Here, the focus shifts from just performance to elements like cost, reliability, and user satisfaction.
Through extensive research, users have often pointed out differentiating factors between Quicke loaders and other brands, such as John Deere or JCB. Key considerations may include:
- Joystick Responsiveness: Quicke's joystick often receives accolades for its immediate feedback and ease of control compared to other models, which can feel sluggish or unresponsive.
- Durability: Many farmers have noted the longevity of Quicke joystick parts even when subjected to harsh conditions encountered in fields, unlike some competitors’ models which may wear out more quickly.
- User Preference: Surveys indicate that operators who have experience with multiple brands frequently prefer Quicke for its intuitive layout, making the learning curve less steep for new users.
Ultimately, these comparative analyses allow potential buyers to make informed decisions based on firsthand accounts and detailed observations. Field performance and comparisons highlight the importance of selecting a joystick that can withstand the demands of agricultural work while supporting operator proficiency and satisfaction.
User Experiences and Feedback
Understanding user experiences and feedback is a crucial aspect of evaluating Quicke loader joystick systems. This section provides insight into the practical implications of joystick design and functionality as perceived by actual users. Their testimonies reveal valuable information about how these systems operate in real-world conditions, contributing to better future designs and increasing user satisfaction.
As feedback is received from a diverse array of users, including farmers and agricultural professionals, it reflects a wide spectrum of needs and expectations. Addressing user experiences aids in identifying key elements that impact functionality, reliability, and comfort. This understanding helps manufacturers to refine their products while encouraging potential buyers to make informed decisions based on real-world applications.
User experiences can lead to improvements in joystick ergonomics, software interfaces, and overall functionality. Collecting and analyzing feedback is essential for innovation, ensuring that joystick parts meet the evolving demands of the agricultural sector.
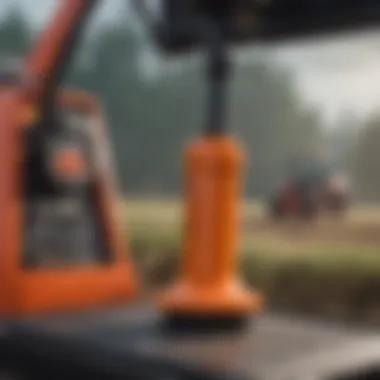
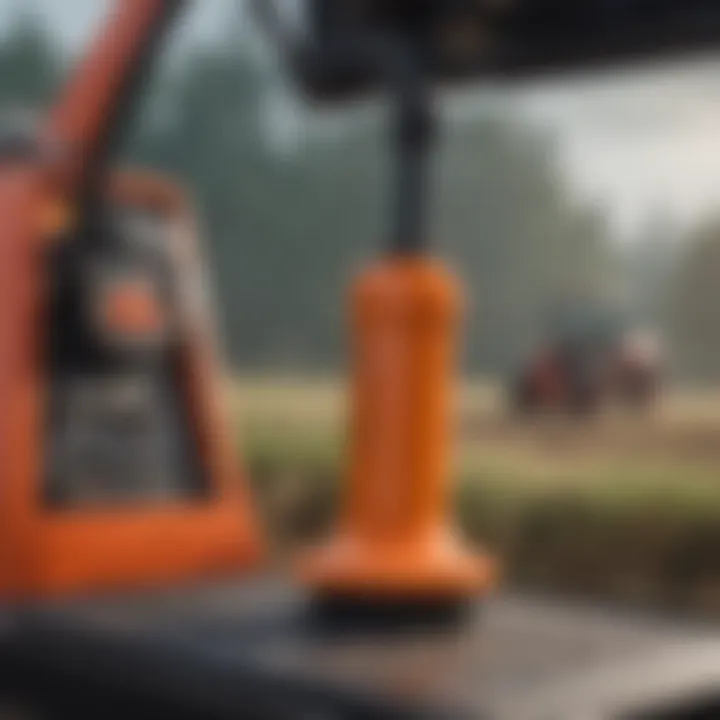
User Testimonials
User testimonials offer a direct perspective of the performance regarding Quicke loader joysticks. Many users appreciate the intuitive nature of joystick controls, noting how easy it is to manipulate the loader with precision. Some testimonials highlight that the joystick’s design allows for smooth and immediate response, making operational processes much more efficient.
For example, one user remarked,
"Using the Quicke joystick has transformed how I handle my loader. The responsiveness is remarkable, and I can perform tasks that previously took much longer."
However, not all feedback is universally positive. Some testimonies point to challenges encountered with system calibration and responsiveness in specific models. These concerns underscore the importance of reliable feedback, as they guide both potential users and manufacturers regarding areas needing improvement or adjustment.
Common Complaints and Resolutions
While many users express satisfaction, common complaints do surface. One prevalent issue reported is the difficulty some experience in engaging the joystick in extreme weather conditions. Cold temperatures can affect the movement resistance, leading to less user comfort.
To address these complaints, manufacturers can consider enhancing material properties to ensure consistent performance regardless of external conditions. Solutions may also include user-guides that suggest how to adjust joystick sensitivity or alternatives for extreme environments.
Another common point of feedback is related to the electronic components used within the joystick systems. Users sometimes mention malfunctioning sensors that may lead to unexpected operational behaviors. Ensuring robust electronic circuit designs can minimize such disruptions and enhance longevity.
By actively addressing user complaints, manufacturers can significantly improve user satisfaction and loyalty. Engaging users in the feedback process fosters a strong community around the product, further enriching the insights gained from collective experiences.
Environmental Considerations
In the realm of agricultural equipment, the significance of environmental considerations cannot be overlooked. As farmers and manufacturers navigate an increasingly eco-conscious market, the impact of joystick systems used in Quicke loaders plays a pivotal role in both operational effectiveness and ecological sustainability. This section delves into two crucial aspects: sustainability in manufacturing and the emissions associated with joystick design.
Sustainability in Manufacturing
The production of joystick parts involves a complex interplay of materials and processes. To minimize environmental impact, manufacturers must prioritize sustainable practices. This includes selecting materials that are recyclable or sourced from sustainable origins. For instance, using recycled plastics and metals not only reduces waste but also lessens the overall carbon footprint.
Moreover, the adoption of energy-efficient manufacturing technologies can significantly lower emissions during production. Techniques such as lean manufacturing aim to optimize resource use, which results in reduced waste. Companies can integrate renewable energy sources, such as solar and wind power, into their operations, thereby minimizing reliance on fossil fuels.
In recent years, several firms have initiated programs to evaluate their supply chains. Understanding the environmental impact of each component can guide improvements in sourcing and production methods. By fostering a culture of sustainability within manufacturing, the industry can contribute positively to environmental conservation efforts while addressing the needs of modern agriculture.
Impact of Joystick Design on Emissions
Joystick design directly affects the efficiency and emissions of the machinery it controls. Innovative designs can enhance the ergonomics of operation, thus reducing energy wastage and improving productivity. For example, advanced sensors and electronic circuitry in joystick systems can facilitate more accurate and responsive controls. This leads to optimized hydraulic performance and reduced fuel consumption.
When considering emissions, it is essential to examine the operational environment of Quicke loaders. The integration of smart technology can also play a key role. Smart systems can monitor performance metrics and suggest operational adjustments that significantly cut down emissions during usage. This is especially critical for equipment working in sensitive environments, where pollution can have pronounced effects on agriculture and local ecosystems.
Key Point: Smart joystick systems not only improve user experience; they actively contribute to reducing overall emissions through precise control and monitoring.
Future Directions in Joystick Development
As the landscape of agriculture evolves, the design and functionality of joystick systems for Quicke loaders are likewise expected to undergo significant transformations. Addressing future directions in joystick development is crucial as it combines the need for effective equipment operation with the advent of technological advancements. This section elaborates on the emerging trends and potential innovations that may redefine joystick performance in upcoming years.
Predicted Trends
The future of joystick technology will likely be shaped by several key trends. These include:
- Integration with Digital Platforms: Joysticks will increasingly connect to digital platforms for real-time data analysis, allowing operators to monitor performance metrics and machine productivity.
- Enhanced Ergonomics: The focus on user comfort will drive the development of joysticks designed with ergonomic shapes and features, reducing operator fatigue during long hours of use.
- Wireless Technologies: Expect to see more joystick systems that operate without physical connections, enabling greater flexibility and reducing wear and tear on components.
- Customization Options: Farmers may demand greater customization for joystick controls, allowing adjustments based on specific machinery and tasks. This move would enhance user experience and boost productivity.
The implications of these trends are profound. They not only signify a leap in user experience but also enhance the overall performance and reliability of Quicke loaders.
Potential Innovations
Innovation will be at the forefront of joystick development. Several areas warrant close attention:
- Smart Sensors: Future joysticks may include advanced sensors that monitor not only the position of the joystick but also the operator's actions. This feedback could allow for quicker adjustments and improved response times.
- Artificial Intelligence (AI) Integration: AI can analyze operator movements and suggest optimal configurations for specific tasks. This could lead to more intuitive control systems that adapt to the user's style.
- Sustainable Material Use: The push for sustainability could encourage the use of eco-friendly materials in joystick manufacturing. This change would align with larger trends in agriculture toward reducing environmental impact.
- User-Interface Innovations: Graphics and displays integrated into joystick systems might enhance user interaction. For instance, touch-sensitive panels could allow for direct control over various loader functions, offering a modern touch to traditional operations.
The advancements in joystick technology not only improve efficiency but also contribute to a more sustainable and user-friendly agricultural practice.
Finale
The conclusion serves as a critical part of any analytical article. In this article, it encapsulates the discussions around Quicke loader joystick parts while weaving together the intricate details examined throughout the text. This section emphasizes the essential role that joystick components play in ensuring efficient operation and superior user experience in modern agricultural practices. With a focus on functionality, maintenance strategies, and appropriate selection, the conclusion reinforces the articles significance in guiding users in understanding these systems better.
Summary of Key Points
In summary, several key points are highlighted regarding Quicke loader joystick parts:
- Functionality: Joystick systems are pivotal for controlling loaders efficiently, involving various components like control levers and electronic circuitry.
- Maintenance: Regular inspections and proper cleaning are essential to enhance the longevity and reliability of joystick parts.
- Selection criteria: Emphasizing compatibility, quality, and supplier reliability is crucial when selecting parts to avoid operational issues and ensure optimal performance.
- Emerging technologies: The evolution of sensor technologies aids in developing joystick systems that integrate smoothly with modern smart agriculture solutions.
More than just components, joystick parts enhance the overall functionality of farming equipment, ensuring that operators can perform tasks with precision and ease. This ensures that Quicke loaders remain competitive in an industry that constantly demands more efficiency and technological advancement.
Final Thoughts on Joystick Utility
Farmers, by investing in high-quality joystick parts, can expect improved operational efficiency and reduced downtime from equipment failures. Therefore, moving forward, it is essential to stay updated on industry developments and consider how innovations can be integrated into existing systems to enhance performance further.
"A well-maintained joystick system is the linchpin in maximizing the functionality of agricultural loaders, ensuring the swift completion of tasks with minimal complication."