Understanding the Stationary Hammer Mill
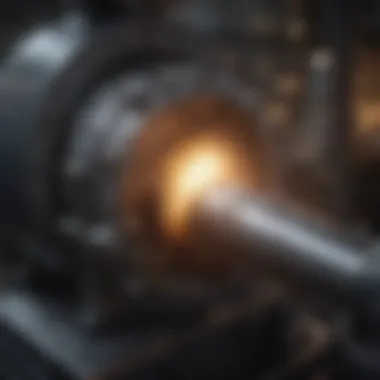
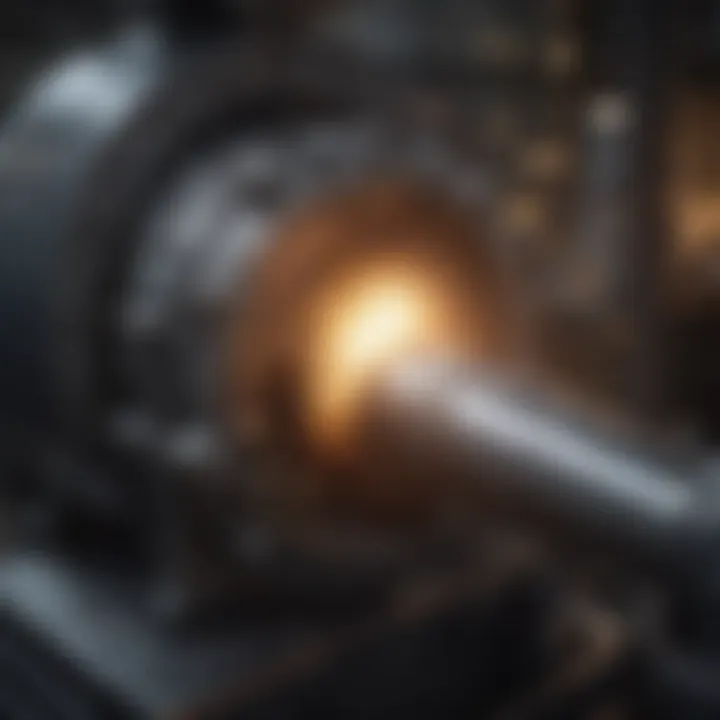
Overview of the Topic
Definition and Importance
A stationary hammer mill is a vital piece of equipment in both agricultural and industrial sectors. At its core, it consists of a series of hammers, typically mounted on a rotating shaft, which pulverize feed materials into finer particles. This machine is crucial not just for its operational efficiency, but for its role in optimizing the processing of various materials, including grains and wood chips. In agriculture, for example, hammer mills enable farmers to process crop residues, which can then be used for animal feed or composting.
The significance of stationary hammer mills cannot be overstated; they serve as linchpins in enhancing productivity while ensuring that materials are processed uniformly. As the world leans more towards sustainable practices, these machines are positioned as key components in waste reduction and resource recovery strategies.
Current Trends
Today, the scene is brisk with innovation. A noticeable trend is the shift towards eco-friendly designs, with manufacturers focusing on materials and technologies that reduce environmental impact. Moreover, the integration of smart technology offers new possibilities, where operators can monitor performance metrics in real-time. Such advancements not only boost efficiency but also prolong the lifespan of the machinery.
Another wave in the industry concerns modular designs. They allow for better adaptability to different operational scales and materials. This adaptability may be particularly appealing to small-scale farmers who often face unique challenges in accessing efficient processing equipment.
Key Techniques and Practices
Step-by-Step Guide
- Understanding Material Characteristics: Before selecting a hammer mill, understanding the physical and chemical properties of the material to be processed is crucial. Different materials may require adjustments in the mill’s configuration to achieve optimal results.
- Setting Up the Hammer Mill: Proper setup is essential. Ensure the mill is leveled and anchored securely. The feeding mechanism should facilitate smooth grain flow without bottlenecks.
- Adjusting Hammer Speed and Screen Size: The speed of the hammers greatly influences the texture of the output. Slower speeds may yield coarser particles, while faster speeds might produce finer ones. Use the appropriate screen size to achieve the desired granulation.
- Monitoring Performance: Keeping an eye on operational metrics such as power consumption and output particle size can help identify issues early. Regular checks can also assist in maintaining equipment longevity.
- Regular Maintenance: An undeniably important step, maintenance should include cleaning, lubricating parts, and checking for wear and tear on the hammers and screens. A well-maintained hammer mill can keep performing optimally for years.
Tools and Equipment Needed
To effectively utilize a stationary hammer mill, various tools and equipment are useful:
- Safety gear (gloves, goggles)
- Loading equipment (e.g., conveyors or augers)
- Quality control devices (moisture meters, particle size analyzers)
- Maintenance tools (wrenches, grease guns)
Challenges and Solutions
Common Obstacles
While stationary hammer mills are robust machines, they are not without challenges:
- Wear and Tear: Frequent use can lead to hammers and screens wearing out, affecting performance.
- Contamination Risks: If not cleaned properly, cross-contamination can lead to quality control issues.
- Variable Material Sizes: Inconsistent sizes of input materials can lead to inefficient processing and increased energy consumption.
Innovative Solutions
To tackle these issues, the following strategies may prove beneficial:
- Regular Monitoring Systems: Implementing technology that alerts operators when hammers need replacement can prevent sudden downtime and optimize performance.
- Strict SOPs (Standard Operating Procedures): Establishing and adhering to cleaning protocols minimizes contamination risks significantly.
- Customizable Settings: Opting for hammer mills with adjustable settings allows for better handling of diverse material inputs, thus enhancing efficiency.
"A well-structured approach to managing these challenges can propel your processing operations to a new level of efficiency."
The objective here is clarity of operations, reliability of outcomes, and sustained productivity in the context of agricultural and industrial applications.
Prologue to Hammer Mills
Hammer mills play a pivotal role in the world of material processing, especially in agriculture and related industries. Understanding this equipment is essential since it contributes significantly to efficiency and productivity. It allows for the breakdown of various materials, paving the way for improved processing and more effective transformation of raw inputs into valuable products.
Modern agriculture—replete with challenges—demands innovative solutions. Hammer mills have proven their worth by providing reliable options for processing grains and other materials. For instance, in grain processing, they efficiently reduce the size of grains to facilitate more uniformity in subsequent treatments, such as milling or pelleting. This simple yet effective machinery can significantly impact labor efficiency and resource management, making it a topic worth exploring.
From farmers to agronomy professionals, understanding the basics, functioning, and advantages of hammer mills provides insights into how they can enhance agricultural operations. This segment serves as a stepping stone towards grasping the in-depth workings of stationary hammer mills and better equips readers to make informed decisions about their utilization.
Definition of Hammer Mills
A hammer mill, in its simplest form, is a mechanical device that reduces the size of materials through impact. It employs a rotating set of hammers mounted on a rotor, which strikes the material against a hard surface, resulting in a reduction of particle size. Hammer mills vary in design, but they generally have one thing in common: they enable efficient processing of a wide range of materials, including grains, wood chips, and even some metal scraps.
This versatility adds to their appeal. Farmers can use them for grain processing or creating animal feed. In industrial settings, they find applications in recycling or wood processing. The definition, however, doesn’t quite capture the complexity that comes with different designs and adaptations each mill can have according to specific processing needs.
History and Evolution
The history of hammer mills is rich and reflects the evolution of both technological advancements and agricultural practices. The earliest hammer mills emerged in medieval times, primarily powered by wind or water. These initial machines served rudimentary needs of agriculture, focusing predominantly on milling grains.
As centuries passed, blacksmiths and innovators improved upon the design, making them more efficient in size reduction capabilities. With the advent of steam power in the 18th century, hammer mills began to see more sophisticated adaptations, leading to increased effectiveness. The introduction of electric power in the 20th century revolutionized the industry, creating a demand for larger and more efficient mills.
Today, thanks to ongoing innovations, we have several types of hammer mills tailored for specific applications. This historical progression not only highlights the ingenuity of past generations but also emphasizes the relevance of such technology in today’s agricultural framework, underscoring the need for a comprehensive understanding of stationary hammer mills.
Understanding Stationary Hammer Mills
Stationary hammer mills stand as crucial components in various agricultural and industrial processes, streamlining the way material is handled and processed. Understanding these machines goes beyond just technical specs; it’s essential for optimizing performance and efficiency. By delving into the working principle and main components, operators and enthusiasts gain insights that improve their operations and decision-making.
Working Principle
The heart of a stationary hammer mill is its ability to crush and grind materials through a series of rapid impacts. The process starts when raw materials enter the mill. It typically operates on the principle of mechanical impact, where hammers, often mounted on a rotor, rotate at high speeds. As they spin, these hammers strike the material repeatedly. This motion breaks down the product into smaller, more manageable pieces. The combination of speed and impact forces results in efficient reduction of material size, making it ideal for various applications like feed production and recycling.
Moreover, the granulation of the product can often be controlled by adjusting settings such as the speed of the rotor and the size of the screen mesh used. This adaptability ensures that materials are processed to meet specific requirements for size and texture, offering tailor-made solutions depending upon the end-use.
Key Components
The functionality of a stationary hammer mill rests heavily on its main components. Each plays a distinct role that contributes to its overall efficiency and performance.
Rotors
Rotors are integral to the operation of hammer mills as they house the hammers and drive the crushing process. The design of the rotor is paramount; a well-designed rotor enhances the hammer's ability to effectively reduce material size. Typically, rotors are precision-engineered, making them resilient to wear. The effectiveness of the rotor improves with its speed, allowing for rapid processing and optimal output.
Key Characteristic: The rotor's speed and mass directly affect the mill's processing capabilities. A heavier rotor tends to handle larger material loads more efficiently.
Benefits: An efficient rotor translates into high throughput rates, making it a favored choice in productive operations. However, if not balanced correctly, it can lead to vibration issues that complicate maintenance.
Hammers
Hammers are the workhorses of the hammer mill, doing the actual grinding and crushing of the material. They usually come in various shapes and sizes, which allows flexibility depending on the application. Regular hammer replacements or reshaping is necessary as they wear down from the impact with materials.
Key Characteristic: The weight and shape of the hammers can change how materials are impacted. For instance, heavier hammers may break tougher materials more effectively, while lighter ones can provide a smoother grind.
Advantages: Hammers that are specifically designed for particular materials can greatly enhance processing efficiency. However, there’s a trade-off; heavier hammers can require more energy to operate.
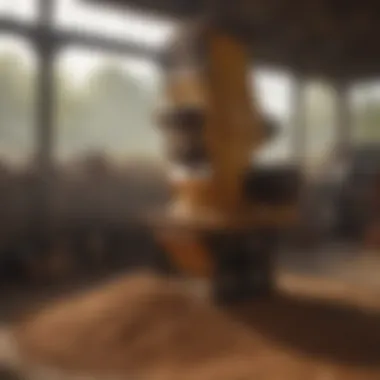

Supporting Structure
The supporting structure of a stationary hammer mill is essential for ensuring stability and safety during operation. This includes the housing, stands, and any necessary framework that holds the components in place. A robust structure minimizes vibrations and noise, promoting smoother operation.
Key Characteristic: Durability and resistance to wear are crucial, as milling involves considerable mechanical stress.
Benefits: A well-designed and sturdy supporting structure can extend the lifespan of the machine and provide safe operation. However, if improperly designed, it can lead to maintenance challenges and safety risks.
In summary, understanding the intricacies of stationary hammer mills, from their working principles to the key components, is vital for professionals in agriculture and other industries. This knowledge not only enhances operation effectiveness but also aids in selecting the right machine for specific processing needs.
Applications of Stationary Hammer Mills
The realm of stationary hammer mills is vast, extending their usefulness across a myriad of applications that cater to both agricultural and industrial needs. The importance of understanding how these machines integrate into different sectors cannot be overstated. Their capacity to reduce materials efficiently, coupled with the versatility in processing various substances, makes hammer mills an invaluable asset. Exploring these applications sheds light on the myriad benefits they offer, allowing professionals to make informed decisions regarding equipment selection based on specific use cases.
Agricultural Use Cases
Grain Processing
In grain processing, stationary hammer mills play a pivotal role by breaking down grains into smaller, more manageable sizes. This specific aspect is crucial as it enhances the efficiency of subsequent processing steps, such as milling and baking, which are foundational in food production. The key characteristic of grain processing through hammer mills lies in its ability to produce uniform particle sizes. This uniformity allows for better feed efficiency in livestock and improved end-product quality in food.
The effectiveness of hammer mills in grain processing is due to their high-speed hammers that chop and grind grains. A unique feature of this process is the ability to adjust the sieve size, enabling operators to customize the output to meet varying requirements. While there are numerous advantages, like enhanced digestibility for animal feed and improved flour quality for baking, it’s important to acknowledge the potential drawback of overheating the products during processing. Proper calibration of the equipment and monitoring can mitigate such issues, ensuring that the benefits outweigh any disadvantages.
Animal Feed Production
Animal feed production is another crucial application of stationary hammer mills. Here, they create well-balanced feed mixtures that significantly boost livestock health and productivity. The key characteristic of animal feed production using hammer mills is their ability to process a diverse range of ingredients, from grains to protein sources like soybean meal. This capability makes them a popular choice in the agriculture sector.
One outstanding aspect of animal feed production is the consistency achieved in the final product. The fine grinding achieved through hammer milling ensures that all components are evenly distributed, preventing nutrient segregation. However, the finer the grind, the less structured the feed might be, which can be seen as a disadvantage from the perspective of livestock needing roughage to aid digestion. Operators must balance the feed’s texture and nutrient concentration to ensure optimal animal health.
Industrial Applications
Wood Processing
In industrial settings, wood processing stands out as a significant application for stationary hammer mills. These machines efficiently reduce wood waste into manageable chips or sawdust, which can then be repurposed in various ways, including biomass fuel or raw materials for particleboard. The key characteristic of wood processing with hammer mills is the machine’s capability to handle large volumes of wood materials.
This mass reduction is beneficial as it not only minimizes waste but also enhances the overall efficiency of the wood recycling process. Some unique features, like adjustable screen sizes and varying hammer designs, allow for tailored processing depending on the wood type and desired final product. On the flip side, operators must ensure that maintenance is performed regularly to prevent clogging and damage that can stem from processing resinous woods.
Recycling
Recycling is a critical application of stationary hammer mills, playing a substantial role in waste management and resource recovery. Fixed hammer mills are particularly effective in breaking down materials like plastics, metals, and organic waste. The key characteristic of recycling using hammer mills is their capacity to handle a wide variety of materials, which is essential for efficient waste processing.
What sets recycling through hammer mills apart is the environmental benefit they provide—reducing waste going to landfills while recovering valuable materials. They can produce a homogeneous mix, making sorting and further processing easier down the line. However, the challenge comes with certain contaminants that may affix to the materials, posing potential wear issues or even damage to the machinery. Practicing proper material pre-sorting is thus crucial to maximize effectiveness in recycling applications.
Advantages of Stationary Hammer Mills
The advantages of stationary hammer mills can't be overstated when considering their impact on both agricultural and industrial operations. These machines are a key player in the processing of various materials, however, it's essential to look closely at some of the specific benefits they offer. Let's dive into a few of the standout advantages that make stationary hammer mills worthy of attention.
Efficiency in Material Reduction
Stationary hammer mills are renowned for their efficiency in reducing the size of diverse materials through impact. As material is fed into the mill, high-speed rotating hammers strike the material, fragmenting it into smaller pieces. This process is not just fast; it’s also effective.
Some key points to consider regarding efficiency include:
- Rapid Processing: Hammer mills minimize the time between input and final product, making them ideal for operations requiring quick turnaround.
- High Throughput: These mills are designed to handle a large volume of material with consistent quality, ensuring that production doesn’t lag.
- Uniform Particle Size: Achieving a consistent size is crucial for next-stage processing, particularly in animal feed production, as it affects digestibility and nutritional value.
"Efficiently reducing material size is crucial for maximizing productivity and ensuring high-quality end products."
Versatility in Processing
Another notable advantage of stationary hammer mills is their versatility. They can handle a wide range of materials, from grains and seeds to wood and plastic. This makes them incredibly valuable in various industries. Here’s a closer look:
- Diverse Material Compatibility: Hammer mills can be adjusted to process different materials, including soft and hard substances. Whether you’re in agriculture or recycling, there’s a fit for your needs.
- Adaptable Settings: Adjusting the speed and the configuration of the hammers allows for customized processing of materials, enhancing their usability across application fields.
- Integration with Other Equipment: Hammer mills often can be paired with other processing equipment, creating seamless workflows that enhance overall production capabilities.
Cost Effectiveness
When we talk about financial considerations, stationary hammer mills shine. They not only reduce operational expenses but also add value in various ways:
- Lower Energy Consumption: Despite their powerful performance, stationary hammer mills are designed to be energy-efficient, thus lowering operational costs.
- Reduced Labor Costs: With their capacity to process large volumes quickly, these mills require less manual labor, which can result in overall savings.
- Long-lasting Durability: The robust design and materials used in constructing these machines lead to reduced maintenance costs over time, giving them a longer lifespan.
Design Considerations
When it comes to stationary hammer mills, the design is not just a matter of aesthetics or features. It fundamentally affects performance, efficiency, and output quality. Thoughtful design considerations make a world of difference, determining how well the machine can handle different materials, and whether it operates within optimal ranges of efficiency. Here, we’ll parse through some pivotal aspects to mull over when designing or selecting a hammer mill for varied applications.
Size and Capacity
The size and capacity of a stationary hammer mill are crucial. They dictate how much material can be processed at a given time, directly influencing the overall productivity of the operation. Larger mills might seem like the obvious choice, promising higher throughput; however, they also come with higher energy requirements and often entail more maintenance.
Misjudging the appropriate size can lead to underperformance or, conversely, overloading. For example, if a farmer opts for a hammer mill that is too small for their operations, they may find themselves continually running the mill at full capacity, leading to quicker wear on the equipment and, ultimately, costly repairs. On the flip side, investing in a larger mill that remains underutilized can waste resources and result in excessive energy costs.
Thus, one must evaluate the expected workload, the kind of materials to be crushed, and the desired output. This assessment enables the selection of an appropriately sized mill, striking a balance between capacity and efficiency.
Material Composition
The materials used in the construction of hammer mills determine their durability and performance. A hammer mill made from high-quality material is less prone to wear and tear, crucial for maintaining consistent output and minimizing downtime.
For instance, milling tough materials requires robust hammers and a well-designed feed structure. If the mill is built with materials that cannot withstand sustained use, it may lead to frequent breakdowns, frustrating any operation.
Moreover, understanding the materials being processed can also influence design. For instance, if your feedstock includes materials with varying shapes or densities, like straw and harder woods, the mill might need particular adaptations to handle them effectively.
"Choosing the right composition keeps your operations seamless and reduces surprises down the road."
In short, not paying attention to material composition during the design phase may compromise not only production rates but also the safety and longevity of the mill itself.
These design considerations serve as the backbone upon which effective and efficient milling operations are built. By closely examining both the size and capacity, alongside the materials used in construction, professionals can select or design stationary hammer mills that meet their specific needs in either agricultural or industrial settings.
Maintenance and Care
Proper maintenance and care of stationary hammer mills is essential to maximize performance, prolong lifespan, and ensure safety during operations. These machines, fundamental to both agricultural and industrial processes, require diligence from operators and technicians alike. Regular maintenance not only prevents unexpected breakdowns but also enhances the efficiency and output of the equipment.
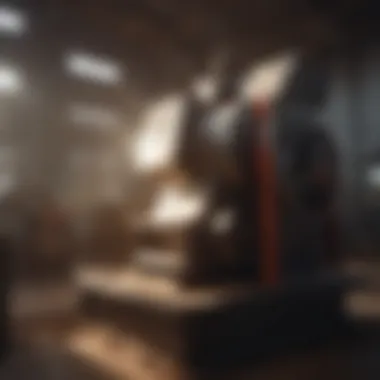
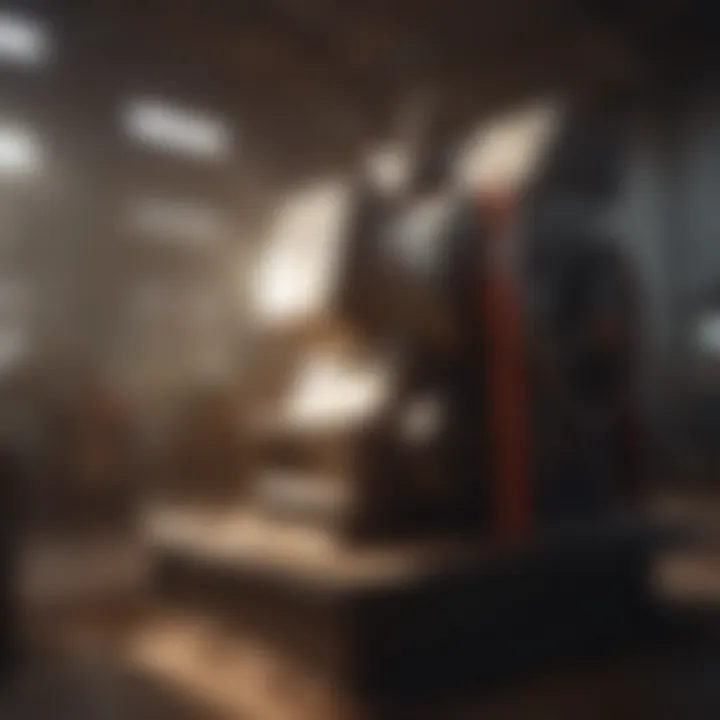
By attending to maintenance, operators can notice improvements in productivity. For instance, a well-maintained hammer mill runs smoother, leading to more consistent particle size and a better quality end product. Additionally, neglected equipment is prone to developing problems that can escalate, leading to costly repairs or worse, extended downtime.
Regular Maintenance Practices
Establishing a routine maintenance schedule is vital for the longevity of a stationary hammer mill. Here are some best practices to consider:
- Daily Checks: Operators should inspect the mill's exterior, looking for any visible wear and tear or leaks.
- Lubrication: Keeping moving parts well-lubricated—like the bearings and shafts—is essential. Over time, lubrication may diminish, leading to increased friction and wear. Ensure to refer to manufacturer recommendations for appropriate lubricants.
- Hammers Inspection: Consistently checking the condition of the hammers helps in identifying wear early. Worn hammers may need reshaping or replacement to maintain efficient functioning.
- Screen Examination: Screens should be monitored for wear since they are critical in determining the particle size of the output. Make sure to change any damaged or excessively worn screens promptly.
- Belt and Drive Maintenance: Ensure belts are properly tensioned and free from cracks or significant wear. Any imbalance can cause excessive strain on other components, leading to premature wear.
Indicators of Wear
Identifying indicators of wear is critical for timely maintenance and effective operation of a stationary hammer mill. Here are key signs to watch for:
- Increased Noise: If the operation suddenly becomes louder than usual, this could suggest wear in components like bearings or hammers.
- Frequent Blockages: A rise in material blockages might indicate the screen or hammers have lost their effectiveness.
- Variability in Output: If the consistency of the output material changes, it may signal uneven wear or damage in the hammers or screens.
- Power Consumption: A sharp increase in power usage could suggest mechanical resistance due to wear, requiring immediate attention.
- Physical Damage: Regular inspections can reveal cracks or deformities in the structure or components of the hammer mill, which should be repaired or replaced as needed.
"Regular maintenance is not just a chore; it’s an investment in productivity. Ignoring it could have you scrambling to fix problems after they arise, rather than working smartly to prevent them."
Safety Measures
Safety measures in the context of stationary hammer mills play a critical role in ensuring the well-being of operators and the longevity of the machinery. These machines, while incredibly efficient at processing materials, come with inherent risks that necessitate clear protocols and guidelines. Failing to observe proper safety measures can result not only in costly damages to the machinery but also in severe injuries to personnel. Hence, comprehending and applying safety standards is paramount for every operator and organization involved.
Operational Safety Protocols
Operational safety protocols ensure that every individual working with a stationary hammer mill understands the risks and knows how to minimize them. Some of these protocols include:
- Personal Protective Equipment (PPE): Operators should always wear appropriate PPE including helmets, safety goggles, gloves, and protective footwear. This basic gear significantly reduces the likelihood of injury from mechanical components or materials.
- Training and Certification: Operators must undergo thorough training. This training should cover machine operation, maintenance, and safety procedures to ensure that they are well prepared to handle any situation. Refresher courses and certification updates are equally important.
- Machine Guards: Guards on rotating parts are essential. They prevent accidental contact with moving parts and should always be in place before the machine is started.
- Power Lock-Out/Tag-Out (LOTO): Before servicing or clearing jams, the machine must be completely powered down and locked out. This means that nobody can inadvertently turn the machine back on while someone is working on it.
Implementing these safety protocols not only promotes an atmosphere of responsibility and care but makes the workplace smoother and more efficient.
Emergency Procedures
Every facility operating stationary hammer mills should have a comprehensive set of emergency procedures set in stone. These procedures ensure that, in case of an incident, the response is swift and efficient. Key elements include:
- Emergency Stop Mechanisms: Ensure that all operators know where the emergency stop button is located, and they can access it easily. This can drastically reduce injury during a crisis.
- First-Aid Kits: Well-stocked first-aid kits must be easily accessible. Additionally, have personnel trained in basic first-aid procedures on-site to deal with minor injuries immediately.
- Fire Safety: Operating a hammer mill introduces a risk of fire from sparks or overheated components. Fire extinguishers that are easily accessible and regularly inspected are crucial. Employees should know the evacuation plan in case of a fire.
- Incident Reporting: All incidents, regardless of severity, must be documented and reviewed. This practice helps identify weaknesses in protocols and adjust training or procedures accordingly.
Implementing these emergency procedures not only prepares operators for the unexpected but ensures that a culture of safety pervades the workplace, thereby protecting everyone involved.
"Safety doesn't happen by accident. It happens by design."
Sustainability in Hammer Milling
Sustainability in hammer milling is a pivotal aspect that resonates throughout this article. As industries become more aware of their environmental footprint, the focus on sustainable practices increases. Hammer mills, while primarily designed for material processing, can also contribute significantly to broader environmental goals. By emphasizing energy efficiency and waste reduction, these machines can support agricultural and industrial practices that are not just effective but also responsible.
Energy Efficiency
Energy efficiency is a key pillar in promoting sustainability within hammer mill operations. As energy costs continue to rise, farmers and businesses are seeking ways to optimize their machinery to achieve better outcomes without breaking the bank. Stationary hammer mills can be specifically designed to operate at lower energy levels while maintaining high performance. This is achieved through various design considerations, including:
- Optimized motor sizing: Properly sized motors reduce excess energy consumption, ensuring just the right amount of power is used for the required task.
- Variable speed drives: These allow operators to adjust the speed according to the material being processed, leading to reduced energy usage.
- Aerodynamic designs: The design of the rotor and other components can minimize air resistance, further lowering energy requirements.
To illustrate,
"A study conducted on a stationary hammer mill in a grain processing facility showed a 30% reduction in energy consumption when operating at optimized motor speeds compared to standard settings," highlights recent research on grinding efficiency.
Waste Reduction Strategies
When it comes to waste reduction, hammer mills can play a transformative role. As byproducts and waste materials are processed effectively, it leads to significant reductions in waste generation. Here are some strategies that can be employed:
- Utilization of byproducts: Many agricultural operations can repurpose waste materials from hammer milling. For instance, the residuals from grain processing can be transformed into quality animal feed, hence reducing overall waste.
- On-site recycling: By integrating additional machinery, like pellet mills, alongside stationary hammer mills, businesses can create a closed-loop system. The offcuts and leftover materials from one process can feed directly into another, minimizing waste.
- Education and training: It’s crucial to invest time in training operators on best practices for waste management. When team members understand the significance of efficient processing, they can actively contribute to reducing waste and enhancing sustainability.
In summary, integrating sustainability into hammer milling operations promotes not only ecological benefits but also economic advantages. By focusing on energy efficiency and waste reduction strategies, agricultural and industrial stakeholders can engage in more sustainable practices, ensuring that processes are both effective and responsible.
Technological Advancements
In today's fast-paced world, the significance of technological advancements in hammer milling cannot be understated. These developments play a pivotal role in enhancing productivity, reducing costs, and improving the overall efficiency of the milling process. As the demands within agricultural and industrial sectors grow, the evolution of these machines has kept pace, offering innovative solutions that address modern challenges head-on.
Automation in Hammer Mills
Automating hammer mills marks a transformative shift in the way these machines operate. With automation, operators can expect more consistent outputs and minimized human error. This is particularly crucial in settings where precision is key. For example, in animal feed production, the correct particle size greatly affects the nutritional value. An automated system can constantly monitor and adjust the settings to ensure the desired grain size is achieved.
In practical terms, the impact of automation can be seen in several areas:
- Real-time Monitoring: Sensors can provide valuable data regarding material flow and thickness, allowing operators to make immediate adjustments.
- Remote Operation: Many newer hammer mills come with remote oversight, enabling operators to manage various systems from a distance and swiftly address any disruptions.
- Energy Efficiency: Automation systems can optimize energy consumption, leading to cost savings. For instance, by adjusting operation speeds according to the material being processed, a mill can operate at peak efficiency without wasting energy.
With the ongoing push for smart agriculture, automation is likely to become a staple in hammer milling, transforming not just efficiency, but the very nature of operational standards within the industry.
Smart Milling Solutions
Smart milling solutions embody the integration of advanced technology with traditional milling practices. These systems utilize artificial intelligence and machine learning to enhance decision-making processes and outcomes. The result? More intelligent, adaptable machines that respond in real-time to variabilities in operation.
Consider a scenario where a hammer mill is processing diverse materials. A smart milling solution could identify the unique characteristics of each material—be it moisture content, density, or size—and adjust the milling parameters accordingly. This adaptability can lead to:
- Optimized Performance: Different materials require distinct handling. By adjusting the mill’s configurations automatically, the performance and quality of the output can be significantly enhanced.
- Predictive Maintenance: Smart systems can not only monitor performance but also predict when maintenance is due. This minimizes downtime, ensuring operations continue smoothly.
- Data Analytics: By compiling and analyzing data from mill operations, farmers can derive actionable insights to enhance production processes.
"The future of hammer milling lies in leveraging technology to create systems that learn, adapt, and optimize performance, making operations more efficient."
Comparative Analysis
When it comes to choosing a hammer mill, understanding the nuances between stationary and portable options is pivotal for optimizing efficiency and productivity. This section shines a light on critical comparisons while making a case for why a deeper look into these machines can aid in smarter decision making.
Stationary vs. Portable Hammer Mills
Stationary hammer mills are large, robust machines designed for high-capacity tasks typically located within a manufacturing facility. They often boast greater durability and longevity compared to their portable counterparts, which may lack some of the heft needed for heavy-duty applications.
- Durability:
A stationary mill can weather the storm of consistent production. Their sturdy design usually means less wear and tear over time. - Capacity:
When you need to process bulk materials, stationary options generally have superior throughput. This makes them ideal for large operations where efficiency is paramount. - Versatility:
While stationary mills are great for bulk processing, portable mills often shine in situations where flexibility is key. Farmers who move between fields might benefit from the mobility of portable mills, making them a solid choice for smaller operations. - Cost Considerations:
Stationary mills often come with a heftier price tag upfront. However, over time, their durability can justify the investment through reduced maintenance and replacement costs.
In summary, the choice between stationary and portable hammer mills often boils down to specific operational needs. It's worth weighing advantages carefully against limitations.
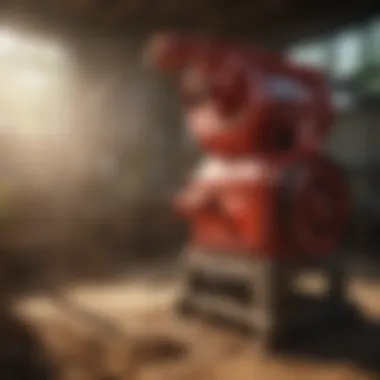
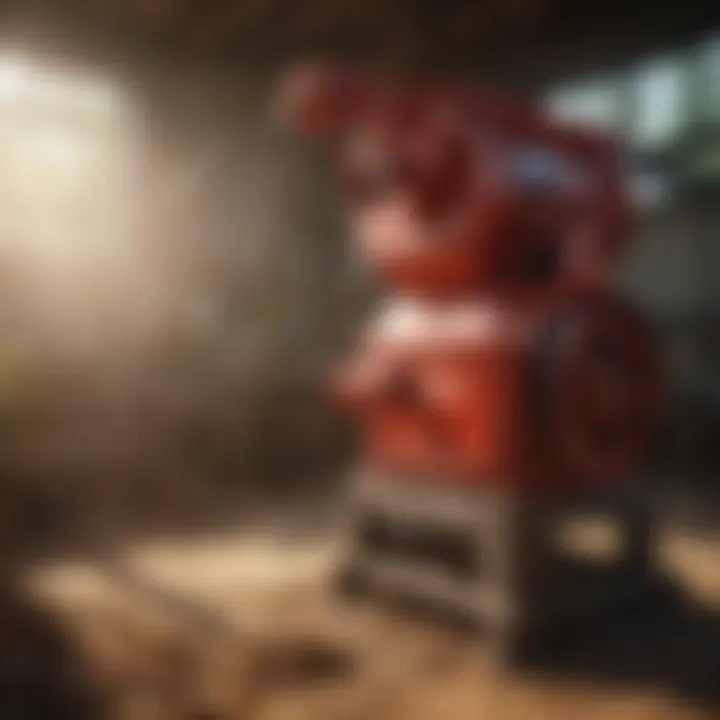
Cost Analysis Overview
Understanding the cost structures associated with hammer mills is essential for financial planning in any agricultural or industrial setup. Cost analysis is not merely about initial purchase price; it's about the entire lifecycle of the machine.
- Initial Investment:
- Operational Costs:
- Replacement Parts and Repairs:
- Resale Value:
- Stationary mills tend to have higher acquisition costs compared to portable models, reflecting their robust construction and larger capacity.
- These include energy consumption, labor utilization, and maintenance. Stationary machines, equipped for higher processing volumes, can sometimes offset their purchase price through efficient operation.
- The frequency of repairs and part replacements can drive costs up significantly. Stationary hammer mills, being more durable, might require less frequent replacements than portable ones, which are sometimes more susceptible to damage during transport.
- The market often appreciates stationary mills for their longevity. Conversely, portable models might depreciate faster due to their wear during transit.
Understanding these costs and their implications can be critical when making a long-term investment in milling equipment.
Future Trends in Hammer Milling Technology
The landscape of hammer milling technology is constantly shifting, driven by advancements that aim to increase efficiency, sustainability, and functionality. Particularly in agriculture, the trends that emerge resonate through the entire supply chain, impacting productivity and economic viability. Understanding these trends provides a lens through which one can appreciate how future innovations will shape the use of stationary hammer mills and, consequently, the broader agricultural field.
Emerging Technologies
The tide is turning with the introduction of cutting-edge technologies that enhance both the performance and versatility of stationary hammer mills. One significant advancement is the integration of IoT (Internet of Things) devices. This technology permits real-time monitoring of machine performance and efficiency, enabling operators to make informed adjustments on the fly.
For instance, utilizing sensors to monitor energy consumption can drastically help predict maintenance needs before they become a costly headache. This extends the machine's lifespan and reduces downtime. Furthermore, software designed for predictive maintenance engages operators to streamline processes, allowing them to maintain optimal performance levels quickly.
Another vital area of development is in material science. Innovation in the types of materials used for making hammers and rotors has resulted in more robust and durable tools. High-strength alloys and advanced coatings can withstand more severe wear and tear, leading to enhanced efficiency and better processing capabilities. This reflects a growing commitment to durability and effective material processing in the industry.
Industry Expectations
Looking toward the future, industry experts project a shift toward more sustainable practices within hammer milling. There's a consensus that environmental responsibility will become a non-negotiable criteria for both consumers and producers. As such, hammer mill manufacturers are under pressure to develop machines that prioritize energy efficiency.
Moreover, as the global market increasingly focuses on environmental impacts, end-users will expect in-depth transparency from suppliers about the sustainability of their equipment. This expectation touches on everything from energy consumption metrics to the sourcing of raw materials used in production.
"The future of hammer milling technology is closely tied to an industry-wide shift towards sustainability and efficiency."
As farmers and agricultural professionals become more aware of their environmental footprint, they will likely favor companies that align with their values. Embracing eco-friendly technologies not only meets this demand but can also enhance brand loyalty in competitive markets.
With demands for improved sustainability, the industry will also expand its horizons regarding bio-based materials—encouraging the exploration of alternative raw materials that can potentially replace conventional inputs in the hammer milling process.
Case Studies
Case studies play a crucial role in demonstrating the practical applications and real-world effectiveness of stationary hammer mills, particularly in agricultural and industrial contexts. By analyzing specific instances where these machines have been implemented, we can gather invaluable insights that underscore the benefits and considerations in selecting and utilizing such equipment. This section highlights two main facets: Successful Implementations and Lessons Learned.
Successful Implementations
One standout example of successful implementation comes from a mid-sized corn milling operation in Iowa. The facility invested in a high-capacity stationary hammer mill to enhance grain processing efficiency and output quality. The mill not only improved the rate of grain reduction but also allowed for better control over the consistency of the final product. This operational upgrade enabled the facility to meet growing demands in a way they never could with their older equipment.
In another case, a large timber processing company in Oregon adopted a stationary hammer mill for wood scrap reduction. The same mill that reduces timber by-products has significantly decreased waste disposal costs while turning excess material into usable wood flour. This has opened up new revenue streams for the company as they can now sell this by-product in various industries.
Lessons Learned
From these implementations, several key lessons have emerged:
- Importance of Proper Sizing: It’s vital to ensure the hammer mill's size aligns with the expected production capacity. Mismatches can lead to inefficiencies that negate the benefits of upgrading from older models.
- Maintenance Awareness: Regular maintenance cannot be overlooked. In both cases, companies realized that proactive maintenance schedules extended the life of their hammer mills, optimizing operational efficiency.
- Training for Operators: Ensuring that operators are thoroughly trained in the nuances of the hammer mill is essential. Inexperienced handling can lead to misoperations, impacting both safety and productivity.
- Customization Options: Adapting the equipment to specific processing needs can enhance performance. Companies that modified their machines to better suit their materials found improved output and reduced operational headaches.
These case studies provide a lens into the real-time impact of adopting stationary hammer mills, illustrating not just their capabilities, but also the path to effective implementation and operation. They highlight the necessity of learning from past experiences, which is vital for any operation looking to maximize its efficiency and sustainability in processing.
Expert Insights
Understanding the role of stationary hammer mills in various sectors is crucial for professionals engaging with these machines. In this section, we delve into the perspectives and insights from seasoned experts who have spent years in the field, examining the nuances that define the operational success of hammer mills. Their experiences inform not just best practices but also the importance of selecting the right machinery for specific applications.
The significance of gathering expert insights lies in the complex nature of hammer milling. It's not only about choosing the right mill but also about understanding how these machines fit into a larger operational framework. Professionals glean valuable information on design optimization, maintenance schedules, and efficiency enhancements directly from those who have navigated these challenges firsthand.
Interviews with Industry Leaders
Interviews with industry leaders provide an invaluable accumulation of knowledge that can guide both new entrants and veterans alike. Through their narratives, experts elaborate on how technological advancements have changed the landscape of hammer milling.
For instance, one prominent leader highlights the shift towards automated controls in modern hammer mills, allowing for precision in processing that was unattainable in earlier models. They emphasize:
"Embracing automation is not just about keeping up; it's about staying ahead. The mills can now adjust settings in real-time based on feed characteristics, optimizing output without the usual trial-and-error approach."
Moreover, leaders advocate for creating strong relationships with manufacturers. This ensures that operators reap the benefits of ongoing support and access to spare parts, which are essential for maintaining efficiency. Establishing such connections is often described as a game-changer, setting apart those who prioritize proactive maintenance from those who face unexpected downtimes.
Recommendations for Best Practices
When it comes to hammer milling, adhering to best practices is paramount to achieving operational excellence. Industry experts consistently recommend the following:
- Regular Training: Equip operators with knowledge about the machines. Continuous training can lead to higher productivity and fewer errors.
- Maintenance Scheduling: Implement a regular maintenance schedule based on usage patterns and manufacturer recommendations to prolong the life of the mill.
- Performance Monitoring: Keep an eye on metrics such as throughput and energy consumption. Understanding these figures can help operators identify potential inefficiencies.
- Feedback Mechanism: Establish a system where operators can report issues or share improvements on processing techniques. This continuous loop of feedback can lead to innovative solutions that enhance operations.
Integrating these best practices ensures that hammer mills function optimally and in alignment with the overarching goals of the agricultural operation. For those invested in both agricultural productivity and sustainability, the insights and recommendations provided here form a solid foundation to work from.
Culmination
In wrapping up our exploration of stationary hammer mills, it’s crucial to understand their significance in both agricultural and industrial landscapes. The smooth operation of these machines plays an indispensable role in processing materials efficiently. By streamlining tasks from grain milling to recycling wood chips, stationary hammer mills stand as versatile tools that simplify and enhance production.
Recap of Key Points
To summarize the core takeaways from this guide:
- Understanding Mechanisms: We covered the intricate working principles of stationary hammer mills, ensuring that users comprehend how these machines effectively break down materials through impact.
- Applications: The vast range of applications was highlighted, showing their utility in agriculture for grain processing and livestock feed production, as well as their role in industrial recycling and wood processing.
- Advantages: From energy efficiency to cost-effectiveness, the positive attributes of hammer mills were examined, demonstrating their significance in practical settings.
- Design Considerations: Key components were explored, including size, capacity, and material composition, focusing on how these elements influence performance and maintenance requirements.
- Future Trends: Emerging technologies and expected advancements in hammer milling were discussed, showcasing the potential for innovation and improvement in the industry.
By engaging with these elements, professionals in agriculture and industry can make more informed decisions regarding the selection and utilization of stationary hammer mills.
Final Thoughts
As we draw this guide to a close, it’s clear that stationary hammer mills are more than just heavy machinery; they are pivotal in shaping the efficiency and sustainability of material processing across various sectors. For farmers and agricultural enthusiasts, the choice of a hammer mill can significantly impact productivity and cost management.
Investing time in understanding these machines pays off, especially with the constant advances in technology and processing techniques. Adopting best practices in operation and maintenance ensures that these machines serve their purpose effectively, prolonging their lifespan while maximizing output.
Understanding how these machines function and their operational context will not only enhance productivity but also contribute to a more sustainable agricultural and industrial future.
Exploring this evolving landscape promises numerous opportunities, pushing the boundaries of what can be achieved in the realms of agricultural efficiency and industrial productivity.