Comex Welding Caps: Safety and Functionality Explained
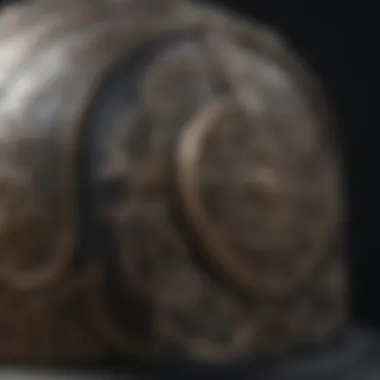
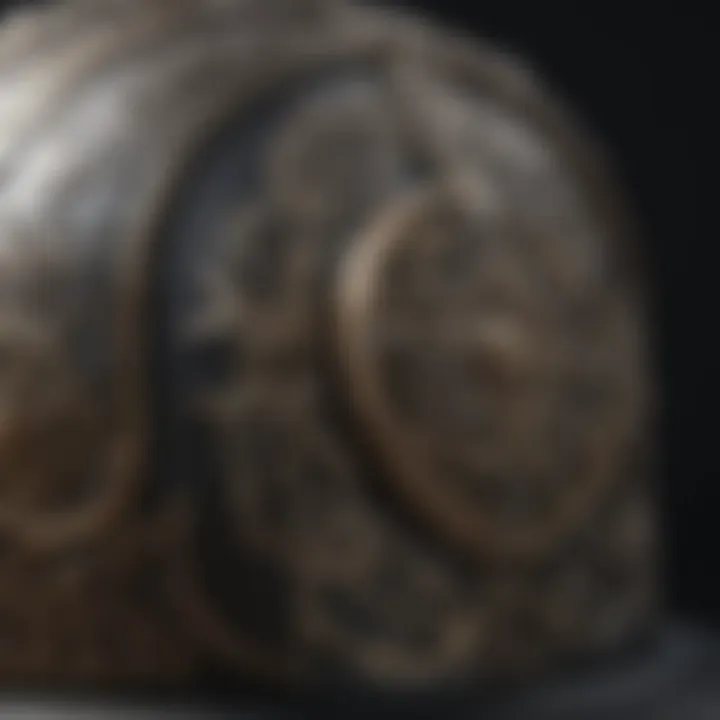
Overview of the Topic
Definition and Importance
Welding caps are protective headgear specifically designed for welders. They serve a critical function in safeguarding professionals from heat and sparks produced during welding processes. Comex welding caps, in particular, stand out due to their unique designs tailored for various welding environments. Proper head protection is essential, as it ensures safety and enhances the efficiency of welders by preventing distractions caused by potential hazards.
The significance of wearing suitable protective gear cannot be overstated. Welders expose themselves to extreme conditions, including intense heat and bright light. As such, Comex welding caps not only provide physical protection but also contribute to overall comfort while working.
Current Trends
In recent years, there has been a noticeable shift in the materials used for welding caps. Many manufacturers, including Comex, are exploring lightweight and breathable fabrics to enhance wearer comfort. Innovations such as moisture-wicking materials have also been integrated to manage sweat and temperature more effectively.
Furthermore, the aesthetic appeal of welding caps is gaining attention. Many welders favor caps that reflect personal styles or organizational branding. As companies strive to create a more inclusive workplace, the focus on customizable design options is becoming increasingly relevant. This trend reflects a broader movement towards personalization in professional attire, encouraging welders to express their individuality.
Key Techniques and Practices
Step-by-Step Guide
Selecting the right Comex welding cap involves several considerations:
- Purpose: Identify the specific welding process being used. Different processes may require varying levels of protection.
- Fit and Comfort: Ensure that the cap fits snugly but comfortably. An ill-fitting cap can be a distraction during critical tasks.
- Material: Look for caps made from flame-resistant materials. Additionally, breathable fabrics enhance comfort during prolonged use.
- Style: Consider different styles available. Some may prefer a fitted cap, while others might opt for a more traditional form.
Finding the right Comex welding cap can greatly improve safety and performance on the job.
Tools and Equipment Needed
While selecting a Comex welding cap is vital, it's equally important to have the right supplementary items:
- Safety Goggles: Protect the eyes from harmful UV rays.
- Leather Gloves: Safeguard the hands from heat and sharp materials.
- Welding Jacket: Provides additional protection for the torso.
These items work collectively to create a safer environment for welding tasks.
Challenges and Solutions
Common Obstacles
Despite the many benefits of Comex welding caps, challenges still exist. One of the primary issues is ensuring the cap remains properly positioned during heavy work. A cap that moves can lead to reduced protection.
Another challenge is managing sweat and heat buildup, particularly in warmer environments. This can distract a welder and impact their performance.
Innovative Solutions
To address these challenges, some innovative solutions include:
- Adjustable Straps: Many caps now feature adjustable designs that keep the cap securely in place, even during vigorous activity.
- Better Ventilation: Features such as mesh panels or moisture-wicking linings can help regulate temperature and improve comfort.
"The right welding cap not only protects your head but also contributes to your overall focus and performance on the job."
By choosing the right Comex welding cap and understanding the challenges that may arise, welders can enhance their safety and improve their work efficiency.
Preface to Comex Welding Caps
Welding is a critical process in various industries, and safety is a paramount concern for welders. Comex welding caps stand out as essential protective gear for individuals engaged in this high-risk profession. The importance of understanding these caps lies not only in their protective qualities but also in their contribution to overall welding effectiveness and comfort.
Definition and Purpose
Comex welding caps are specifically designed to provide a protective barrier for welders' heads. They serve multiple purposes, including heat resistance, shielding from sparks, and improving the wearer's comfort during extended working hours. The caps are made with fabrics that can withstand high temperatures, protecting welders from potential injuries. Additionally, the design of the caps often includes features such as moisture-wicking properties to ensure that welders can focus on their tasks without the distraction of discomfort or sweat.
Historical Development
The inception of welding caps dates back to the early days of welding, when the safety concerns of the trade were beginning to be recognized. Initially, welders used makeshift headgear, typically made from materials that offered little to no protection from heat or sparks. Over time, as the risks of welding became more apparent, manufacturers like Comex began to innovate.
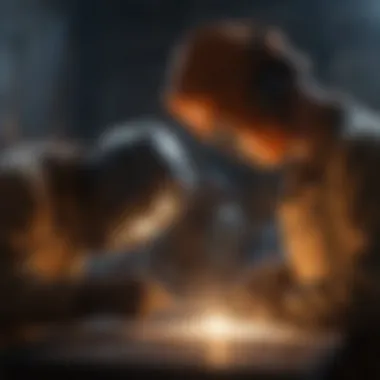
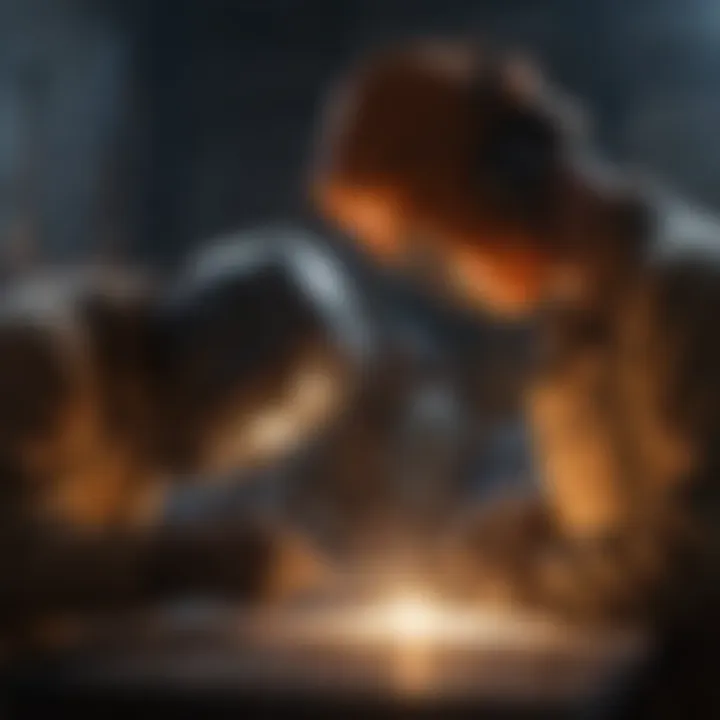
The evolution of Comex welding caps paralleled advancements in welding technology and materials science. Now, these caps are not just functional; they reflect a deeper understanding of the unique needs of welders. Changes in industrial practices and the increased demand for worker safety standards have driven the development of caps that offer improved protection. Through the decades, these caps have evolved into specialized gear that is as much about comfort as it is about safety, ensuring that welders can work effectively in often challenging environments.
"Welders’ caps are not merely accessories; they are an integral component of the safety arsenal that can significantly reduce the risk of injury during operations."
In summary, the understanding of Comex welding caps is rooted in their definition and purpose as well as their historical context. Recognizing the importance of these caps helps to underscore the significant role they play in promoting safety and efficiency in the welding industry.
Key Features of Comex Welding Caps
The effectiveness of Comex welding caps stems from their key features. Understanding these elements gives insight into the functionality and practicality of the caps in various welding environments. It is essential to recognize how materials and design variations contribute to user safety and comfort.
Material Composition
Cotton
Cotton is a traditional fabric used in many welding caps. It is valued for its breathability. This key characteristic allows moisture to escape, helping to keep the wearer cool during welding tasks. Cotton caps tend to be lightweight and comfortable to wear for extended periods. However, a notable drawback is its limited flame resistance. In high-heat environments, this reduces its effectiveness in protecting the wearer.
Polyester
Polyester is another popular material used in welding caps. One of the most important features of polyester is its durability. This characteristic makes it suitable for heavy-duty work environments. Polyester is resistant to wear and tears, thus extending the life of the caps. Moreover, polyester has moisture-wicking properties, which provide comfort to the user. However, it is less breathable compared to cotton. This can lead to discomfort in hot situations.
Other Blends
Other blends incorporate various materials, combining the benefits of cotton and polyester. These blends may enhance breathability while maintaining durability. A distinctive feature of such blending is the balance it provides between comfort and protection. By using other blends, manufacturers create caps that cater to specific needs, though some blends may not perform as well in extreme heat compared to pure cotton or polyester.
Design Variations
Styles
Styles of welding caps significantly influence their usability and preference among welders. There are several designs, such as classic caps and bandanas. Each style offers a unique way to protect the head. For instance, the classic cap provides full head coverage, while bandanas allow greater airflow. However, style choice can be personal and depends on the wearer’s comfort and safety needs.
Sizes
The size of the welding cap is critical for both safety and comfort. A properly fitted cap will protect the head more effectively. There are various sizes available, accommodating different head shapes and dimensions. It is a common concern that a cap that is too loose may not stay in place, while one that is too tight can cause discomfort. Hence, selecting the right size is crucial.
Customizations
Customizations can enhance the functionality of welding caps. Some manufacturers offer options such as adjustable straps or personalized designs. This customization allows users to have better control over the fit and style of their caps. Moreover, customizations can include personalized logos or names, making them popular in professional settings. However, custom features can also lead to increased costs, which is something to consider for budget-conscious buyers.
Functional Benefits of Using Comex Welding Caps
Comex welding caps serve a crucial role in ensuring the safety and comfort of welders. These caps are more than just protective gear; they offer several functional benefits that enhance the welding experience. Understanding why these benefits are essential can help professionals appreciate the value of using Comex welding caps in various settings.
Heat Protection
Heat protection is one of the primary functionalities of Comex welding caps. During welding processes, operators are often exposed to extreme temperatures. A welding cap acts as a barrier, protecting the scalp and neck from direct heat. The materials used in Comex caps are specifically designed to withstand high temperatures, offering welders peace of mind. Moreover, the caps reduce the risk of burns, which can be severe and require medical attention.
Another point to consider is the way these caps encompass the head. They minimize heat buildup around the head, providing a cooling effect while working in high-temperature environments. This function can be particularly beneficial for long-duration tasks, where prolonged exposure to heat is unavoidable.
"Using Comex welding caps is not just about comfort; it's about enhancing safety in potentially dangerous work environments."
Shielding from Sparks
Welding operations generate sparks that can fly unpredictably during the process. These sparks pose a risk not only to skin but also to hair and eyes. Comex welding caps are designed to offer effective shielding from these sparks. By covering the head fully, the caps protect against hot metal fragments that can cause irritation or injury.
The lightweight and durable fabric of Comex caps limits the chances of sparks penetrating through to the skin. This function is essential in preventing accidents that could result in burns or other severe injuries. Also, some caps have specialized treatments or coatings that enhance their resistance to ignition, further improving safety for welders.
Comfort and Fit
Comfort and fit are pivotal for any piece of safety equipment. Comex welding caps are constructed with the user in mind, providing a snug yet comfortable fit that allows for ease of movement. A well-fitted cap helps prevent slippage, ensuring that it remains in place throughout the welding task. This attention to fit significantly reduces distractions, allowing welders to focus on their work.
Furthermore, many Comex welding caps feature breathable fabric. This is important for maintaining airflow around the head, reducing discomfort caused by perspiration. Being comfortable can improve focus and productivity, critical factors in achieving high-quality welding outcomes.
In summary, the functional benefits of Comex welding caps are significant. By providing heat protection, shielding from sparks, and ensuring comfort and fit, these caps empower welders to perform their tasks more safely and effectively. This overview highlights why Comex caps are an investment in both safety and performance.
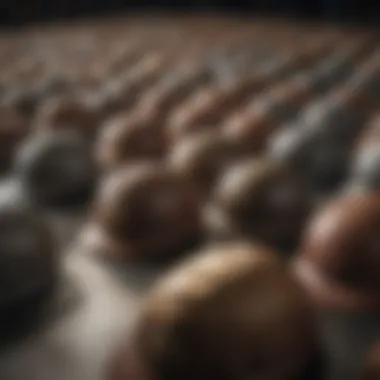
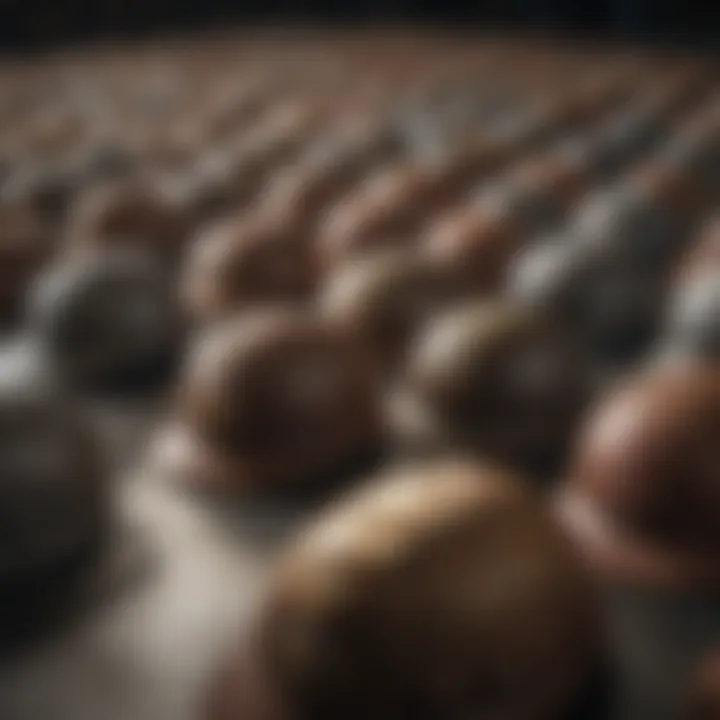
Industry Applications
Welding caps are essential in many professional settings, providing not just comfort but also safety. Comex welding caps are especially notable due to their tailored designs for specific applications. Understanding where these caps are used can guide professionals in selecting the right protective gear for their needs.
Construction
In the construction industry, workers face various hazards related to welding activities. This includes exposure to intense heat, ultraviolet light, and flying debris. Comex welding caps provide much-needed protection against these elements.
The headgear is beneficial for welders who often work in dynamic environments, such as on construction sites, where conditions can change rapidly. Wearing a Comex welding cap helps in shielding the scalp and neck from heat and sparks. Additionally, these caps come in various styles, allowing workers to choose one that fits comfortably under a welding helmet.
Welders can select caps that are made with specific materials to enhance heat resistance. This ensures not just safety but also comfort, which increases efficiency during long working hours. When the right Comex cap is worn, it allows welders to concentrate on their tasks without the distraction of discomfort or safety concerns.
Manufacturing
In manufacturing settings, welding procedures are integral to creating numerous products. Here, the use of Comex welding caps can significantly impact worker safety. Since manufacturing often involves high-volume welding, the risk of exposure to harmful elements persists.
Comex welding caps protect against waste heat and prevent injuries from sparks. Moreover, these caps' lightweight designs facilitate ease of movement, which is crucial when handling large pieces of machinery or equipment.
Additionally, the availability of various sizes and customizations means that welders can choose caps tailored to their specific roles within the manufacturing process. Overall, the use of Comex welding caps in this environment can lead to a reduction in workplace accidents, while also enhancing productivity.
Automotive
The automotive industry is another field where Comex welding caps play a vital role. Here, welders often encounter various challenges, including intricate components and a range of welding techniques. The precision needed in automotive welding means that safety cannot be compromised.
Comex welding caps designed for this industry focus on providing adequate protection without hindering mobility. Given that automotive welders often have to work under significant strain – whether it’s in terms of posture or equipment weight – comfort becomes crucial.
Furthermore, the caps can be beneficial in maintaining a professional appearance while providing functional protection. This is particularly valuable in settings where workers are part of a team, maintaining a collective standard of safety and professionalism.
In summary, Comex welding caps serve an important purpose across various industries, enhancing both safety and productivity for professionals engaged in welding activities.
Choosing the Right Comex Welding Cap
Selecting the appropriate Comex welding cap is crucial for ensuring safety and comfort during welding tasks. The variances in material, style, and intended use significantly influence the overall performance and experience of the welder. As welding can be a demanding job, especially in terms of heat and sparks, choosing the right cap can not only enhance protection but also improve work efficiency. In this section, we will explore important aspects to consider when making this choice.
Assessing Specific Needs
Before acquiring a Comex welding cap, it is important to identify your specific needs. Different welding environments may call for unique features in caps. For example, if you are frequently working in high-temperature settings, prioritize caps made from heat-resistant materials. Additionally, consider whether you need extra coverage for your neck or ears, depending on the welding techniques employed.
Key points to assess include:
- Types of welding performed (MIG, TIG, Stick)
- Location of the job site (indoor vs outdoor)
- Duration and frequency of use
Such considerations will guide you in selecting a cap that provides adequate protection and comfort.
Evaluating Quality Standards
Once you understand your needs, the next step is to evaluate the quality standards of Comex welding caps. Quality is essential to ensure that the cap can withstand the rigors of welding work. Look for certifications and test results that adhere to industry safety regulations. Caps should also be durable enough to resist wear from sparks and heat exposure.
Factors to focus on include:
- Material strength and durability
- Breathability of fabric
- Resistance to flame or heat
Checking product reviews and feedback from other users can help determine if a cap meets your expected quality standards. This can inform your choice and ensure you invest in a reliable product.
Budget Considerations
Budgeting for a Comex welding cap involves balancing quality and affordability. While it may be tempting to select the cheapest option available, this can lead to compromises in safety and longevity. Investing more in a high-quality cap can save you money in the long run, as it will typically last longer and require fewer replacements.
To effectively consider your budget:
- Set a price range according to your financial constraints
- Weigh the cost against known quality and features
- Look for warranties or guarantees that indicate manufacturer confidence
Maintenance of Comex Welding Caps
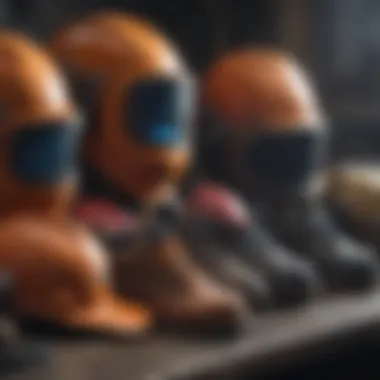
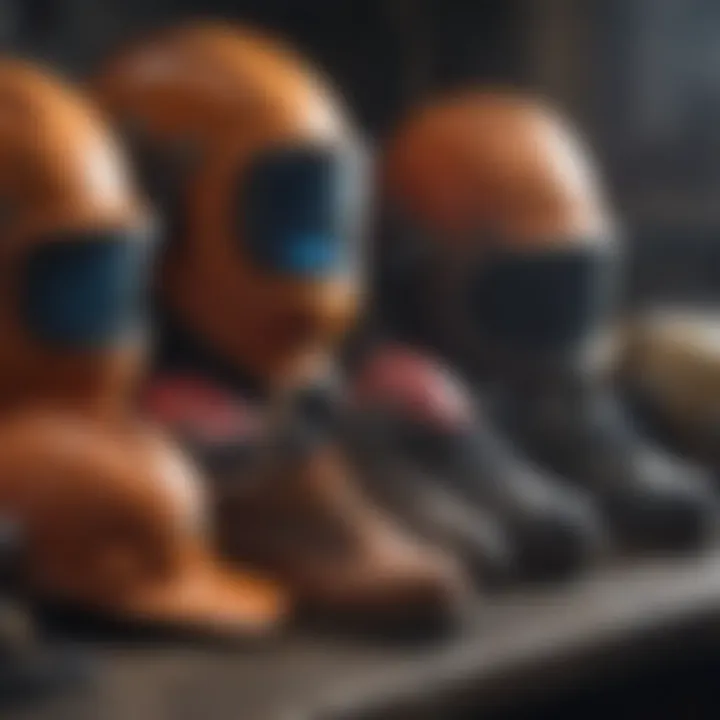
Maintenance of Comex welding caps is essential for ensuring their effectiveness and longevity. Proper care minimizes wear and tear, prolonging the use of these protective gear items. Regular maintenance has its benefits, including safety, hygiene, and cost-efficiency. Inspecting and maintaining welding caps can also foster a positive working environment by ensuring that welders have clean and functional gear while they work.
Cleaning Guidelines
Keeping Comex welding caps clean is vital for several reasons. First, dirt and debris can affect the cap's ability to protect the welder from sparks and heat. Additionally, buildups of sweat and oils can lead to unpleasant odors. To effectively clean a welding cap, follow these guidelines:
- Manual Washing: Hand wash the cap using warm water and mild soap. Avoid harsh detergents to maintain material integrity.
- Machine Washing: If the product allows, wash it on a gentle cycle. Always check the label for instructions.
- Air Dry: Avoid using a dryer, as high heat can damage the cap. Instead, lay it flat on a clean surface.
These steps will help ensure that the caps remain effective and comfortable. Regular cleaning can also prevent health issues related to poor hygiene.
Storage Recommendations
Proper storage of Comex welding caps is just as important as cleaning them. Improper storage can lead to deformation, damage, or contamination. Here are some recommended practices:
- Cool, Dry Place: Store the caps in a cool and dry environment to avoid moisture damage. Humid conditions can lead to mold growth.
- Away from Direct Sunlight: Prolonged exposure to sunlight can degrade the materials used in the caps, so avoid sunny spots.
- Use of Storage Containers: Consider using breathable storage bags instead of plastic, as these allow airflow and help prevent moisture buildup.
By following these guidelines for storage, you will enhance the lifespan of Comex welding caps and maintain their functionality.
"Proper maintenance of welding gear enhances safety and performance over time."
The effectiveness of Comex welding caps is closely linked to their maintenance. By implementing a rigorous cleaning routine and adhering to storage best practices, welders can ensure their gear is ready for rigorous tasks. This proactive approach is a hallmark of responsible safety gear management.
Emerging Trends in Welding Caps
Emerging trends in welding caps are essential to consider for both safety and functionality. This section highlights innovations that are shaping the future of these protective gears, focusing on materials and manufacturing practices. Recognizing these trends allows welders and industry professionals to make informed choices that enhance both safety and comfort during welding tasks.
Innovative Materials
The development of innovative materials is transforming welding caps. Lightweight, durable fabrics are becoming increasingly popular. These materials not only provide comfort but also improve protection against heat and sparks. Examples include heat-resistant silicone blends and advanced fiberglass composites. These materials can withstand higher temperatures without compromising the cap’s integrity.
Additionally, moisture-wicking properties are being integrated into designs. This feature is particularly beneficial in environments where welders may sweat. Fabrics like X-Static® and Coolmax® actively manage moisture, keeping welders dry and comfortable.
Another significant advancement is the use of breathable membranes. Fabrics that allow heat and moisture to escape improve overall comfort. This is crucial for individuals who wear welding caps for extended periods. Improved ventilation can lead to better focus and performance on the job.
Sustainable Manufacturing Practices
Sustainability in manufacturing practices is gaining traction in the production of welding caps. Many companies are now prioritizing eco-friendly materials and processes. This shift addresses the growing demand for sustainability in industry. Brands that adopt these practices often use recycled fabrics and non-toxic dyes. This not only reduces the environmental impact but also appeals to customers who are environmentally conscious.
Moreover, sustainable practices can enhance the overall quality of the products. Eco-friendly materials often undergo rigorous testing for durability and performance. As the industry recognizes this shift, more brands are likely to follow suit, emphasizing the importance of sustainability.
"Adopting sustainable manufacturing not only meets customer demands but also enhances brand reputation."
Safety Standards
In the realm of welding, adhering to safety standards is essential for protecting both the welder and the environment in which they work. Comex welding caps are not simply an optional accessory; they are an integral part of the safety equipment that ensures compliance with various regulations. These standards are set by regulatory bodies to minimize the risk of accidents and injuries while promoting safe working conditions.
Regulatory Requirements
Regulatory requirements for welding safety gear, including caps, are determined by organizations such as the Occupational Safety and Health Administration (OSHA) in the United States and similar bodies worldwide. These regulations stipulate essential features that welding caps must possess to provide adequate protection. For instance:
- Flame Resistance: Caps should be made from materials that resist ignition and prevent flame spread, offering a crucial barrier against spikes in temperatures and sparks.
- Coverage: Caps must adequately cover the head and neck, preventing exposure to harmful fumes and potential burns. The proper fit is vital to ensure that the cap does not obstruct vision or interfere with protective eyewear.
- Cleaning and Maintenance Standards: The ability to easily clean and maintain the caps is also a consideration in regulatory guidelines. Regular upkeep is necessary for the longevity of the caps and for maintaining hygiene levels in a workshop environment.
Meeting these regulatory requirements is not only about compliance but also about fostering a culture of safety within workplaces.
Certifications
Certifications play a pivotal role in indicating that Comex welding caps meet the required safety standards. Various types of certifications may be sought by manufacturers to demonstrate the effectiveness and reliability of their products.
- ANSI/ISEA: The American National Standards Institute (ANSI) and the International Safety Equipment Association (ISEA) offer certifications that authenticate the safety and performance of head protection gear.
- CE Marking: For products in the European Union, CE marking signifies that the welding cap complies with EU health, safety, and environmental protection standards.
- ISO Certifications: The International Organization for Standardization (ISO) offers certifications that can indicate the quality and safety management processes used by manufacturers.
Welders should always look for these certifications when selecting Comex welding caps. The presence of such marks assures end users of the product's compliance with rigorous safety assessments, helping to mitigate risk in hazardous work environments.
Finale
In the world of welding, the significance of protective gear cannot be overstated. Comex welding caps stand out as an essential component in ensuring both safety and comfort for welders. These caps not only provide heat protection but also shield the head from sparks and other hazardous materials commonly associated with welding tasks. The use of welding caps represents an important aspect of workplace safety in numerous areas, such as construction and manufacturing.
Recap of Importance
Comex welding caps embody a thoughtful blend of practicality and protection. Their materials, which often include cotton and polyester blends, are designed to withstand the rigorous demands of welding environments. Most significantly, these caps offer comfort, allowing welders to maintain focus on their tasks without the distraction of discomfort or unsafe conditions. It is clear that integrating protective gear like Comex welding caps into standard safety practices can significantly enhance the overall well-being of welders. Looking back at the insights presented, one can appreciate the multifaceted benefits these caps provide.