Understanding John Deere Loader Hydraulic Lines
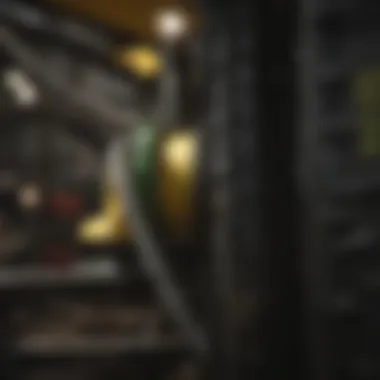

Overview of the Topic
Definition and Importance
Hydraulic lines are crucial components in the operation of John Deere loaders. They play a vital role in transferring hydraulic fluid from the pump to various mechanisms such as the lift arms and buckets. This function enables the loader to perform essential tasks in construction and agriculture, enhancing efficiency and productivity. Utilizing hydraulic lines properly ensures smooth operation, reduced wear and tear on machinery, and overall longevity of the equipment.
The efficiency of the hydraulic system directly impacts the productivity of the loader. When hydraulic lines are operating optimally, they help maintain consistent pressure required for lifting and moving weights. Conversely, any hindrance in this system can lead to delays, as well as increased maintenance costs due to equipment failure. Understanding hydraulic lines is essential for any operator, ensuring that they get the most out of their machinery.
Current Trends
There has been a noticeable evolution in hydraulic technology over recent years. John Deere continues to innovate with hydraulic systems that are more efficient and environmentally friendly. For example, the shift toward biodegradable hydraulic fluids is becoming common. This not only reduces environmental impact but also improves the overall health of the hydraulic systems.
Moreover, advancements in sensor technology allow for real-time monitoring of hydraulic lines. This enables operators to detect potential issues before they escalate, thus optimizing maintenance schedules and minimizing downtime. The integration of smart technology into agriculture machinery is a trend that will likely persist, elevating the operational capabilities of loaders and other equipment.
Key Techniques and Practices
Step-by-Step Guide
- Identify the Type of Hydraulic Fluid Needed: Check John Deere specifications for compatible fluid types. Utilizing the appropriate fluid is crucial.
- Inspect Hydraulic Lines Regularly: Look for signs of wear, leaks, or damage. Ensuring they are in good condition prevents larger issues.
- Replace Worn or Damaged Lines: Follow John Deere guidelines for replacing any compromised hydraulic lines. Using genuine parts is recommended for optimal performance.
- Bleed the Air from the System: After any maintenance, it's essential to bleed the hydraulic lines to remove air pockets, which can cause operational deficiencies.
- Regular Maintenance Checks: Scheduled inspections and servicing can identify potential problems early, reducing the risk of equipment failure.
Tools and Equipment Needed
- Wrenches: For loosening and tightening fittings.
- Hydraulic Hose Cutters: For cutting hoses to the required length.
- Sealant: To prevent leaks at connections.
- Oil Spills Cleanup Kit: To manage any accidental spills.
Challenges and Solutions
Common Obstacles
One common obstacle in maintaining hydraulic lines is understanding when to replace them. Operators often overlook damage, leading to significant failures later. Additionally, finding high-quality replacement parts can be challenging, especially with numerous generic options available.
Innovative Solutions
Developing a checklist for regular inspections can help mitigate these issues. This checklist should prioritize visual inspections and pressure tests to ascertain the state of the hydraulic lines. Leveraging online resources to source genuine John Deere replacement parts is also encouraged. Engaging with the John Deere community on platforms such as Reddit can provide valuable insights and recommendations.
"Timely maintenance and awareness of hydraulic line systems can lead to significantly reduced operational costs and extended machinery lifespan".
Through understanding the intricacies of hydraulic lines in John Deere loaders, operators become empowered to care for their machinery effectively and enhance overall productivity.
Prologue to Hydraulic Systems
Hydraulic systems are pivotal in myriad mechanical applications, particularly in heavy machinery like John Deere loaders. These systems harness the principles of fluid mechanics to generate and control power efficiently. Understanding hydraulic systems is crucial for operators and mechanics alike, as it greatly affects machinery performance and reliability.
Protecting the integrity of hydraulic lines is an essential element in maintaining the operational capabilities of loaders. These lines are responsible for transporting hydraulic fluid, which is fundamental in creating the pressure necessary to perform various tasks like lifting and moving heavy loads.
Key benefits of having a sound knowledge of hydraulic systems include the ability to predict potential failures and the enhancement of routine maintenance. Grasping how hydraulic systems function can lead to improved equipment longevity and productivity within agricultural practices, making this knowledge indispensable for agricultural professionals and enthusiasts.
Basic Concepts of Hydraulics
At its core, hydraulics relies on the principles of fluid mechanics. The fundamental concept is that an incompressible fluid, when pressurized, can transmit force. The Pascal's principle plays a significant role here, stating that pressure applied to a confined fluid is transmitted equally in all directions. This principle is harnessed in John Deere loaders, allowing various components to operate efficiently with relatively low energy inputs.
Hydraulic systems typically consist of several key elements, including a hydraulic pump, fluid reservoir, hydraulic valve, actuators, and of course, hydraulic lines. Each element plays a specific role in ensuring the fluid moves correctly and efficiently throughout the system. Understanding these components helps ensure operators can troubleshoot issues early and maintain optimal functionality.
The Role of Hydraulic Lines
Hydraulic lines are crucial in any hydraulic system as they facilitate the movement of hydraulic fluid between different components. These lines must withstand high pressure and are therefore designed with meticulous care. The materials used for hydraulic hoses must offer durability and flexibility, allowing them to bend around obstacles but resist damage from wear and external factors.
Poorly maintained hydraulic lines can lead to leaks, which not only reduce the efficiency of the system but can also cause safety hazards. An understanding of the role and importance of hydraulic lines helps operators identify symptoms of wear or damage early, thus preventing costly repairs or accidents. Operators who can monitor the status of hydraulic lines will enhance the overall performance of their John Deere loaders and ensure safety during operations.
"Understanding hydraulic lines enhances machinery efficiency and can prevent safety hazards."


In summary, the introduction of hydraulic systems in relation to John Deere loaders covers key concepts that are imperative for successful operation and maintenance. By grasping the underlying principles of hydraulics and recognizing the significant roles played by hydraulic lines, operators and mechanics can engage with their equipment with confidence. The subsequent sections will delve deeper into the specific components and operational mechanisms of hydraulic systems in these versatile machines.
Overview of John Deere Loaders
John Deere loaders play a vital role in modern agriculture and construction. Their efficient operation enhances productivity, making tasks faster and easier. This section will address key aspects of John Deere loaders, shedding light on their features and applications.
Key Features of John Deere Loaders
John Deere loaders are characterized by several essential features that set them apart from other brands. These features enhance their usability and reliability in various tasks:
- Versatility: John Deere loaders are suitable for many applications, from lifting and loading materials to digging and grading. This versatility makes them an indispensable tool on any job site.
- Advanced Hydraulics: The hydraulic systems in these loaders allow for precise control over lifting and handling. This reduces the chance of accidents and improves efficiency.
- Ergonomic Design: Operators comfort is important. John Deere loaders typically have operator stations designed to reduce fatigue. This allows for longer working hours and improved productivity.
- Durability: Built with high-quality materials, John Deere loaders are known for their robustness. They can withstand harsh conditions and heavy use without compromising performance.
- Technology Integration: Many models come equipped with advanced technology, such as telematics, which allows for real-time monitoring of machine performance and maintenance needs.
These characteristics greatly contribute to the effectiveness and reliability of John Deere loaders, making them a preferred choice among agricultural professionals and construction workers alike.
Common Models and Their Applications
Understanding the common models of John Deere loaders helps users select the right tool for specific tasks. Here are some popular models:
- John Deere 244L: This compact loader is designed for landscaping and smaller construction projects. Its agility allows for work in tight spaces.
- John Deere 324L: A mid-size loader, the 324L is optimal for material handling in various applications. It's commonly used in farms and construction sites for transporting loads.
- John Deere 644L: As a larger loader, the 644L is powerful enough for heavy-duty tasks. It is often used in construction, waste management, and agriculture to handle large volumes of material.
Each model serves a unique purpose, and selecting the right one depends on the specific tasks and conditions faced by the operators.
Components of Hydraulic Lines
The hydraulic lines in John Deere loaders serve as the backbone of their operational efficiency. Understanding the components that make up these lines enhances both the durability and functionality of the machinery. This section discusses three critical components: hydraulic hoses, fittings and connectors, and fluid reservoirs and pumps. Each element plays a vital role in ensuring that hydraulic systems perform reliably and effectively.
Hydraulic Hoses
Hydraulic hoses are crucial components that transport hydraulic fluid throughout the system. These hoses must withstand high pressure and are designed to handle the forces generated during operation. The quality of hydraulic hoses significantly influences the performance of the loader. Using subpar hoses can lead to leaks and failures, which can halt productivity and lead to costly repairs.
There are several types of hydraulic hoses, each crafted for specific applications. High-pressure hoses are typically reinforced with multiple layers, while low-pressure hoses might be lighter and more flexible. Pay attention to the pressure ratings when selecting hoses, as exceeding these limits can damage the hose and lead to system failures.
Fittings and Connectors
Fittings and connectors ensure that hydraulic hoses connect securely to various components of the hydraulic system. They play a fundamental role in maintaining the integrity of the hydraulic line. Poorly installed or low-quality fittings can lead to leaks, which may compromise the efficiency of the loader’s operations.
When choosing fittings, consider factors such as the material, size, and pressure rating. For example, using steel fittings offers higher durability than plastic options. It's also essential to match fittings appropriately to ensure a proper seal. Regularly inspecting these connections for wear and damage is an important maintenance practice that can prevent significant issues later.
Fluid Reservoirs and Pumps
Fluid reservoirs and pumps are central to any hydraulic system. The reservoir holds the hydraulic fluid, while the pump generates the pressure needed to operate the system. Choosing the right pump is crucial for ensuring system effectiveness, as it impacts flow rate and pressure. Different models of John Deere loaders may require different specifications for pumps.
Reservoirs must be adequately sized to provide enough fluid for operation while allowing for thermal expansion. A well-designed reservoir will also include features like baffles to reduce fluid turbulence and contaminants. Regular monitoring of fluid levels and condition is essential to maintain appropriate performance levels.
Proper maintenance and understanding of hydraulic lines can significantly extend the life of your John Deere loader.
In summary, recognizing the importance of hydraulic hoses, fittings and connectors, and fluid reservoirs and pumps is vital for the optimal functioning of John Deere loaders. Each component affects the overall reliability and efficiency of the machinery, impacting agricultural operations in substantial ways.
Operation of Hydraulic Lines in John Deere Loaders
The operation of hydraulic lines in John Deere loaders is central to their functionality. Understanding these lines is vital for efficient machinery use in agriculture. Hydraulic lines provide the necessary transfer of pressurized fluid, enabling various functions like lifting and tilting. This section explores the significance of fluid dynamics and control mechanisms relevant to these loaders.
Fluid Dynamics in Hydraulic Systems
Fluid dynamics refers to the behavior of liquid fluids and how they exert forces. In hydraulic systems, the pressurized fluid plays a crucial role in transmitting energy. John Deere loaders utilize this principle to perform various operations.
The efficiency of hydraulic systems relies heavily on how well the fluid flows within the lines. Factors like hose diameter, fluid viscosity, and temperature can affect this flow. For instance, thicker fluids can impede movement, requiring more power to operate effectively.
Key points to consider in fluid dynamics include:
- Pressure Levels: Higher pressure allows for enhanced lifting capability.
- Flow Rate: Determines speed and efficiency; the right size and type of hoses matter here.
- Temperature Control: Overheating can lead to fluid degradation, increasing maintenance needs.
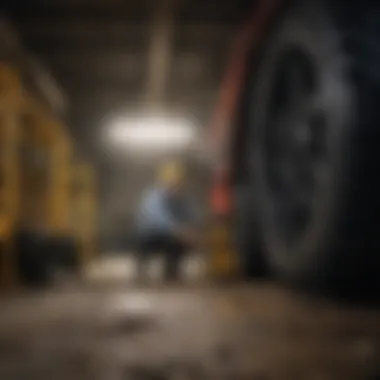

A well-functioning hydraulic system ensures faster operations. It is important to monitor these elements regularly to maintain optimal performance in John Deere loaders.
Control Mechanisms for Loaders
Control mechanisms are essential in managing the operation of hydraulic lines. These devices dictate how the hydraulic fluid is directed throughout the loader’s system. Effective control leads to improved loader functions such as steering and attachment manipulation.
Here are key control mechanisms used in John Deere loaders:
- Valves: Control the direction and flow of hydraulic fluid. Different types include directional control, relief, and flow control valves.
- Actuators: Convert hydraulic energy into mechanical force, enabling loader arms and other attachments to move.
- Sensors: Monitor system pressures and fluid levels, ensuring proper operation and providing feedback for necessary adjustments.
Understanding these mechanisms allows operators to make better decisions during loader operation. For example, knowing when to adjust a valve can enhance performance during challenging tasks. Better control can also reduce stress on the system, prolonging the life of hydraulic components.
In summary, both fluid dynamics and control mechanisms are critical for the seamless operation of hydraulic lines in John Deere loaders. These elements not only enhance machine performance but also contribute to the overall efficiency and longevity of the equipment.
Maintenance of Hydraulic Lines
Maintaining hydraulic lines in John Deere loaders is essential for ensuring operational efficiency and longevity of the machinery. Regular maintenance helps in preventing unexpected failures and costly downtime. Hydraulic lines endure high pressure, and any wear or damage can lead to significant issues. It is vital to monitor these lines closely, as neglect may compromise the functionality of the loader, which is heavily relied upon in agricultural tasks.
Proper maintenance practices contribute to improved performance and safety. By understanding the various elements involved in the maintenance of hydraulic lines, operators can ensure their equipment remains in good working order. This section will delve into routine inspection practices, fluid replacement protocols, and cleaning and flushing systems, all integral to preserving the integrity of hydraulic lines.
Routine Inspection Practices
Conducting regular inspections of hydraulic lines is the first step towards effective maintenance. Operators should examine hoses for signs of wear, cracks, or bulges. Regular visual checks can reveal potential issues before they escalate into serious problems. It is also advisable to check fittings and connections for leaks. Even small leaks can significantly affect system performance and lead to fluid loss.
Some key practices include:
- Scheduled Inspections: Set a routine schedule for inspections based on operation frequency and conditions.
- Document Findings: Keep a log of inspection results to track conditions over time and identify patterns.
- Temperature Checks: Monitor the temperature of hydraulic fluid, as excessive heat can indicate problems in the system.
Fluid Replacement Protocols
Fluid replacement is critical in maintaining hydraulic systems. Hydraulic fluid serves not only as a power transfer medium but also as a lubricant and coolant. Over time, fluid can become contaminated or lose its effectiveness.
To ensure optimal performance, follow these steps:
- Check Fluid Levels: Regularly inspect fluid levels and look for discoloration or contaminants. Low or dirty fluid necessitates replacement.
- Fluid Standards: Use manufacturer-recommended hydraulic fluid to maintain compatibility and efficacy. For John Deere loaders, use products like John Deere Hydraulic Oil.
- Dispose Responsibly: Always dispose of old fluid according to local regulations to minimize environmental impact.
Cleaning and Flushing Systems
Cleaning the hydraulic system helps to remove contaminants that can cause blockages or wear. Flushing the hydraulic lines is necessary when changing fluid or if contamination is suspected.
When cleaning and flushing hydraulic systems, follow these guidelines:
- Use Clean Tools: Ensure all tools and containers used during maintenance are clean to prevent introducing new contaminants.
- Flushing Procedure: Implement a systematic flushing procedure, starting with the component farthest from the reservoir. This helps to push contaminants toward the outlet.
- Check Filters: Don’t forget to check and replace filters during the flushing process to capture contaminants and ensure clean fluid returns to the system.
Regular maintenance of hydraulic lines is not just about routine checks; it is about ensuring safety, efficiency, and prolonging the lifespan of your machinery.
Maintaining hydraulic lines in John Deere loaders involves continuous effort. Using these practices will facilitate early detection of issues and prolong the operational lifespan of the equipment. Farmers and machinery operators should prioritize these maintenance steps to maximize their machinery's performance.
Troubleshooting Hydraulic Line Issues
Troubleshooting hydraulic line issues is a critical aspect of maintaining the efficiency and reliability of John Deere loaders. These machines rely heavily on hydraulic systems to operate effectively. Therefore, understanding how to identify and resolve potential problems can significantly enhance performance and prolong the life of the equipment. Addressing hydraulic line issues promptly reduces downtime, lowers repair costs, and minimizes the risk of serious malfunctions. This section will cover common problems, symptoms that may arise, and techniques for accurate diagnostics.
Common Problems and Symptoms
Hydraulic systems are prone to a range of issues, which can surface through various symptoms. Identifying these symptoms early is key for effective troubleshooting. Some common problems include:
- Leaks in Hydraulic Lines: One of the most frequent issues is fluid leakage. This can occur due to wear on hoses or loose fittings. If you notice hydraulic fluid pooling under the loader or a decrease in fluid levels, it’s essential to inspect the lines immediately.
- Pressure Loss: A drop in hydraulic pressure can lead to sluggish operation of the loader. Symptoms may include inadequate lift capacity or slow response times when controls are engaged.
- Contaminated Hydraulic Fluid: Debris or moisture can contaminate the hydraulic fluid, which may cause erratic operation or increase wear on components. Discoloration or unusual smell of the fluid are indicators of contamination.
- Overheating: If the hydraulic system operates at higher temperatures than usual, it can lead to component failure. Symptoms include abnormal noises and diminished power during operation.
Diagnostics Techniques
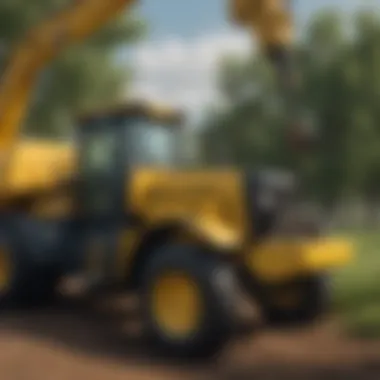

Effective diagnostics are crucial for understanding hydraulic line issues and formulating a repair plan. Several techniques can help identify problems accurately:
- Visual Inspection: Start with a thorough examination of the hydraulic lines, hoses, and connectors. Look for abrasions, cracks, or other signs of wear. Ensure that all fittings are securely tightened.
- Pressure Testing: Use a pressure gauge to check the hydraulic pressure throughout various parts of the system. This test can help detect leaks and areas of pressure loss effectively.
- Fluid Analysis: Conducting an analysis of the hydraulic fluid can reveal contaminants. Samples of the fluid can be sent to laboratories to detect the presence of moisture or particles.
- Temperature Monitoring: Keep an eye on temperature levels during operation. Using thermal cameras or digital temperature gauges could pinpoint hotspots that indicate trouble.
- Systematic Testing: Approach diagnostics systematically. Check each system component, starting from the pump to the actuators, making sure to rule out each part.
"Timely diagnostics not only address immediate issues but also prevent future complications within the hydraulic system."
Proper troubleshooting cannot be overstated. Understanding the types of problems that may arise in hydraulic lines, along with effective diagnostics techniques, ensures that issues are resolved quickly and efficiently. This proactive approach supports long-term functionality and reliability of John Deere loaders.
Upgrading Hydraulic Systems
Upgrading hydraulic systems is an essential process for John Deere loader owners. It ensures that the machinery works efficiently and meets the demands of modern agricultural practices. As technology evolves, the performance expectations for equipment also change. Thus, recognizing when and how to upgrade the hydraulic system can lead to increased productivity and longer equipment lifespan.
Benefits of Upgrading
A well-upgraded hydraulic system provides several benefits, including improved efficiency, enhanced safety, and reduced maintenance costs. Enhanced hydraulic capabilities mean loaders can tackle heavier loads and perform more complex tasks without strain. Additionally, upgrading can lead to energy savings, as modern components are often designed to be more efficient.
Considerations for Upgrading
When considering an upgrade, factors such as compatibility with existing systems, cost implications, and the specific application need to be evaluated. Correctly assessing these aspects can save time and money in the long run.
Identifying Signs for Upgrade
There are several indicators that may suggest an upgrade is necessary for your hydraulic system.
- Decreased Performance
If the loader struggles to lift or operate attachments as it once did, this may indicate inefficiencies in the hydraulic system. - Frequent Maintenance
An increase in leaks, inconsistent responses, or other recurring issues should prompt further investigation into upgrading components. - Technological Advancements
Newer hydraulic systems come equipped with better technology, such as improved control valves and pumps that offer better precision and reliability. If newer models are available, it may be beneficial to consider upgrading.
Technical Considerations for Upgrades
When planning an upgrade for a hydraulic system, several technical aspects should be taken into account:
- Component Compatibility
Be sure that new parts are compatible with the existing system to avoid operational issues. - Fluid Specifications
Different hydraulic fluids work better with certain components. Ensure your fluid type aligns with the new upgrades. - Pressure Ratings
Assess the pressure ratings of the new components. Upgrading to high-performance parts could require changes in pressure settings to prevent system failure.
Ultimately, an effective upgrade not only improves performance but also adheres to safety standards, thereby ensuring the loader operates optimally. Proper planning and analysis will lead to successful integration of upgrades into existing systems.
Safety Protocols for Hydraulic Operations
Safety is paramount in any operation involving hydraulic systems, particularly in heavy machinery like John Deere loaders. The complexity and the potential hazards associated with hydraulic lines make stringent safety protocols essential. Following established safety guidelines not only protects the operator but also prolongs the life of the equipment and improves overall efficiency in agricultural tasks.
Importance of Safety Protocols
Firstly, safety protocols help prevent accidents that can result from hydraulic failures or operator error. A sudden release of hydraulic fluid can have serious consequences, leading to injuries or equipment damage. By adhering to safety protocols, operators can mitigate these risks and create a safer working environment. Additionally, effective safety measures ensure compliance with regulatory standards, safeguarding both the operator and the business from legal repercussions.
Moreover, regular training in safety protocols enhances an operator's knowledge about potential hazards associated with hydraulic systems. A well-informed operator can recognize early signs of trouble, such as unusual noises or fluid leaks, which could indicate a need for maintenance or repairs. Consequently, this proactive approach reduces downtime and boosts productivity.
Personal Protective Equipment (PPE)
Personal Protective Equipment, or PPE, is crucial when operating hydraulic machinery. Depending on the specific tasks, the required PPE may include:
- Safety glasses: Protects eyes from debris and splashes.
- Gloves: Prevents cuts and provides grip when handling components.
- Steel-toed boots: Offers foot protection from heavy objects.
- Hearing protection: Important in preventing hearing loss due to loud machinery.
- High-visibility clothing: Ensures visibility in dynamic work environments.
It is essential for operators to assess the hazards present in their environment and select the appropriate PPE. By doing so, they minimize the likelihood of injury and maintain a focus on operational tasks without distraction from safety concerns.
Emergency Response Procedures
In the event of an emergency involving hydraulic systems, having clearly defined emergency response procedures is vital. Operators should be trained in these procedures to ensure rapid and effective action. Key components of emergency response include:
- Immediate shutdown of machinery: Recognizing when to stop operations can prevent further injuries or damage.
- Communication protocols: Operators must know how to effectively communicate to alert coworkers about the emergency.
- Identifying emergency exits: Familiarity with the layout allows for quick evacuation if necessary.
- First aid training: Basic first aid knowledge can help manage injuries until professional medical assistance arrives.
"Effective emergency response procedures can mean the difference between a minor incident and a catastrophic event."
Regular drills and refresher courses on emergency procedures are fundamental in ensuring that all personnel are prepared in case of an emergency. This preparedness can result in a rapid response that minimizes potential harm and safeguard assets.
Epilogue
Understanding hydraulic lines in John Deere loaders is crucial for maintaining and optimizing the performance of these machines. This article has delved into various aspects of hydraulic systems, emphasizing the integral role hydraulic lines play in the overall functionality of loaders.
In summary, the important elements discussed include the various components that make up the hydraulic lines, such as hoses, fittings, and pumps, and how they interact within the system to facilitate efficient operation. Proper maintenance practices, like routine inspections and fluid replacements, are essential to prevent potential issues that could impact productivity.
Moreover, recognizing the symptoms of hydraulic line problems allows operators to address concerns before they escalate into larger complications. The information presented can help farmers and agricultural professionals understand the significance of timely upgrades to hydraulic systems to meet evolving operational demands.
The benefits of mastering the knowledge about hydraulic lines extend beyond just machinery efficiency. A well-maintained hydraulic system contributes to safety on the job site, reduces equipment downtime, and can enhance the longevity of John Deere loaders. It is important that operators are not only aware of how hydraulic lines function but also the best practices for their upkeep and troubleshooting.
Ultimately, this thorough exploration of hydraulic lines serves as a valuable resource for optimizing the performance of John Deere loaders. Armed with this knowledge, agricultural professionals can confidently approach their machinery, ensuring it operates effectively and safely in the demanding environment of modern farming.